اطلاعات فنی در مورد سقف های عرشه فولادی
مقاله
در مورخ ۱۳۹۶/۰۷/۱۹
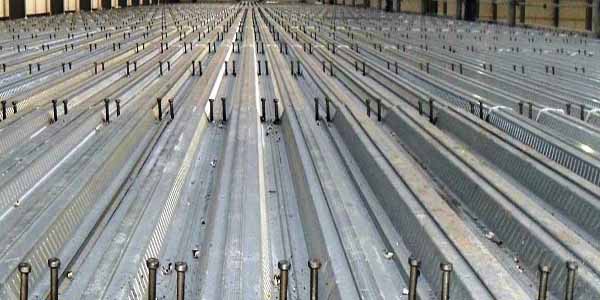
مقاومت در برابر آتش سوزی
ضوابط فصل 8، BS 5950 مربوط به الزامات مقاومت در برابر آتش سوزی باید رعایت گردیده و در محاسبات جداول و نرم افزار وارد شوند.
برشگیر ها در شرایط آتش سوزی
چنانچه مرکب بودن تیر فولادی با دال بتنی روی آن توسط برشگیر ها به میزان کافی فراهم شود آنگاه در زمان طراحی تیر فولادی در برابر آتش سوزی میتوان از وزن دال صرفنظر نمود.
روش های طراحی در برابر آتش سوزی
سه شرط برای طراحی در برابر آتش سوزی وجود دارد:
· مقاومت خمشی در شرایط آتش سوزی
· حداقل عمق دال جهت میزان عایق بودن
· یکپارچگی دال برای محافظت در برابر آتش
ظرفیت دال مرکب در آتش سوزی میتواند با استفاده از روش ساده یا روش طراحی در برابر آتش سوزی بر اساس Eurocodes، محاسبه شود که روش ساده، اقتصادی تر است.
روش ساده
امکان استفاده از روش ساده برای عرشه های تقویت شده و عرشه هایی که بر روی یک تکیه گاه داخلی یا بیشتر که به صورت پیوسته ادامه می یابند، وجود دارد. در این روش تخمین مقاومت در آتش سوزی بر اساس یک یا دو شبکه مش استاندارد می باشد و از هرگونه آرماتور تقویت صرفنظر می گردد.
روش طراحی در برابر آتش سوزی
روش طراحی در برابر آتش سوزی کاربرد کلی دارد.تخمین مقاومت در برابر آتش سوزی بر اساس یک یا دو شبکه مش استاندارد در بالا و یک میلگرد درهرنشیب عرشه می باشد.
در نرم افزار طراحی فرض بر این است که میلگرد دقیقاً در محدوده نشیب عرشه قرار گرفته است برای Light deck 60/80 با یک برجستگی فوقانی د ررأس، میلگرد در زیر آن قرار می گیرد.
محدودیت های خیز
در زمان نداشتن اطلاعات مناسب، باید حدود زیر در نظر گرفته شود:
خیز مرحله ساخت
خیز مرحله ساخت فقط به بارهای مرده بدون ضریب بستگی دارد و بارهای زمان ساخت در نظر گرفته نمی شود. حدود خیز برای قالب بندی در قسمت BS 5950.4 ارائه شده است.
دلیل اصلی محدود کردن خیز در مرحله ساخت، محدود کردن حجم بتنی است که بر روی عرشه قرار می گیرد.افزایش خیزها متأثر از افزایش بتن روی عرشه بوده و این امر باعث افزایش بارهای مرده بر سازه می شود.این خیزها به طور معمول نباید از مقادیر زیر بیشتر شوند:
· بدون در نظر گرفتن بتن روی عرشه LP/180
(که نباید از 20mm بیشتر باشد)
· با در نظر گرفتن بتن روی عرشه LP/130
(که نباید از 30mm بیشتر باشد)
LP دهانه موثر قالب بندی است که کمترین مقادیر :فاصله مرکز به مرکز تکیه گاه های دائمی و دهانه خالص بعلاوه ارتفاع پروفیل می باشد.
مطابق BS 5950، وقتی خیز از DS/10 بیشتر می شود- که در آن DS عمق کلی دال مرکب است –وزن بتن اضافی در حین اجرا به دلیل خیز ورقها باید در محاسبات وزن دال مرکب وارد شود. بنابراین در محاسبات خیز قالب بندی در نرم افزار طراحی فقط وقتی که خیز مرحله ساخت از DS/10 بیشتر شود وزن بتن اضافی در محاسبات منظور می گردد.
در نرم افزار طراحی برای ساختمان های بدون شمع بندی خیز مرحله ساخت مجاز L/130، در نظر گرفته شده است که نباید از 30mm بیشتر باشد. تمام جزئیات و پارامترهای محاسبات در راهنمای نرم افزار طراحی آمده است.
دو مقدار برای خیز دال محاسبه می شود(خیز مرحله مرکب):
· خیز ناشی از بارهای اضافی
· خیز کلی
خیز ناشی از بارهای اضافی
LP/350 (که نباید از 20mm بیشتر شود) و آن خیزی است که دال فقط تحت اثر بار های اضافی از خود نشان می دهد.
خیز کل بار
LP/250 (که نباید از 30mm بیشتر شود)
خیز کلی، خیز دال تحت اثر تمام بارهای اعمالی (شامل تمام بارهای مرده ای که بعد از قرار گرفتن دال وارد میشوند مثل وزن کفسازی، تیغه ها و موارد مشابه)بعلاوه خیز مرحله ساخت می باشد. این مقدار در محاسبات اثرات خزش بتن تحت بارهای مرده و هر خیز اضافی که به دلیل تکیه گاه های موقت (شمع بندی ) ایجاد شده وارد می شود.
ارتعاش
نرم افزار طراحی حساسیت دینامیکی دال مرکب را طبق نشریه SCI P076(راهنمای طراحی ارتعاش سقف) کنترل می کند.فرکانس طبیعی تحت اثر وزن دال ، سقف های کاذب، تأسیسات، کفسازی و10% از بارهای اضافی به جای بارهای دائمی وارد بر سقف، محاسبه می شود.
بارها و ترتیب آنها
بارهای ضریب دار در محاسبات وضعیت حد نهایی لحاظ می شوند که با ضرب مقادیر باره در ضریب اطمینان بدست می آید.
بارهای بدون ضریب در وضعیت حد سرویس دهی و شرایط آتش سوزی، در نظر گرفته می شود. این بارها شامکل وزن دال و بارهای زمان ساخت می باشند که بزرگترین مقادیر :150Kpa و 4.5/LP در نظر گرفته می شود. برای دهانه های چند گانه بدن شمع بندی، بار زمان ساخت 1.5/Kpa فقط بر روی یک دهانه در نظر گرفته شده و در سایر دهانه ها نصف این مقدار(0.7Kpa) لحاظ می گردد.
بارهای ساخت بعنوان بارهای اضافی جهت کنترل در نظر گرفته می شوند. بارهای در نظر گرفته شده در مرحله سرویس معمولی شامل وزن دال و بارهای زنده ومرده اضافی می شود.
مراحل اجرای سقف های مرکب عرشه فولادی
مراحل اجرای سقف های مرکب عرشه فولادی به اختصار به ترتیب زیر می باشد:
1- دپو و انتقال به طبقات : ورق های کامپوزیت پس از انتقال به کارگاه و دپو در یک فضای کوچک ،به کمک نیروی انسانی و بدون نیاز به ماشین آلات و تنها با کمک یک بالابر به تراز های مختلف طبقات منتقل می شود.
2- جا گذاری عرشه های فولادی : این عرشه ها شامل گیره های نر ومادگی هستند که براحتی توسط نیری انسانی نیمه ماهر در یکدیگر چفت می شوند و پس از این مرحله ، رفت وامد در طبقات بسیار ساده میشود و سرعت کار به طرز قابل ملاحظه ای افزایش می یابد.
3- نصب میلگرد و گل میخ : در محلی که عرشه های فولادی برروی تیرها قرار گرفته اند،برای اتصال این دو،از گل میخ استفاده می شود و این عمل باعث کاهش وزن تیرهای فولادی مصرفی می شود.
4- بتن ریزی : پس از اتصال میلگردها، بتن ریزی انجام می شود،ضخامت کم دال و یکنواختی سطح صفحات موجب خروج سریع هوا و ساده تر شدن عمل می شود.
پارامترهای طراحی
عرشه سقف مرکب عموماً با توجه به شرایط مرحله ساخت، بار ودهانه مورد نیاز برای سرویس دهی و مقاومت در برابر آتش سوزی فراهم می شود.
نرخ آتش سوزی
مقاومت= تعیین اندازه شبکه یا فولاد مورد استفاده زیرین
عایق بودن= تعیین حداقل عمق دال
از آنجا که عرشه همانند یک پوسته رفتار می نماید یکپارچگی همواره فراهم می باشد.
خواص صوتی ساختمان
با در نظر گرفتن مقدار ضخامت دال نرخ عایق بودن در برابر صوت انتخاب می شود.
ارتعاش
مسبت دهانه به ضخامت دال همانند وضعیت تیرهای تکیه کاهی در طراحی ارتعاش موثر است.
وزن بتن
وزن بتن، حداقل عمق دال و دهانه را در زمان بتن ریزی تحت تأثیر قرار می دهد.
دهانه عرشه (بدون شمع بندی)
اندازه تیر و فاصله تیر ها از هم، دهانه عرشه را تعیین می نماید.
دهانه عرشه (دارای شمع بندی)
برای استفاده کامل از خواص دال مرکب ممکن است نیاز به شمع بندی موقت باشد.
طراحی دو مرحله ای
همه سقف های مرکب باید در دو مرحله در نطر گرفته شوند.
1- بتن مرطوب/مرحله ساخت
بار به تنهایی توسط عرشه تحمل می شود.
خیزها ناشی از بار بتن، بتن روی عرشه و بارهای ساخت می باشد.
خیز کلی سیستم ناشی از خیز تیرها می باشد.
2- بتن سخت شده/مرحله مرکب
بار توسط دال مرکب تحمل می شود.
خیزها ناشی از تغییر مکان تکیه گاههای موقت (شمع بندی) در صورت وجود، بارهای اضافی و خیز تیرها در نظر گرفته می شود.
هدف کلی طراحی
معمولاً طراحان ترجیح می دهند تا نیاز به شمع بندی موقت را کاهش دهند در نتیجه دهانه و عمق مورد نیاز دال در انتخاب عرشه کنترل کننده می باشد.
معمولاً الزامات آتش سوزی تعیین کننده عمق دال می باشند و برای بیشتر حالتهای بدون شمع بندی، بارهای اضافی روی دال طراحی را محدود نمی کند.
مش ضد ترک (آرماتور حرارتی)
جهت کاهش ترک های ناشی از لنگر خمشی موجود در سقف آرماتورهای تقویتی مورد نیاز بر روی تیرهای تکیه گاهی تعبیه می شوند.
قوانین(BS Pt4) به عنوان معتبرترین ضوابط کنترل ترک های ناشی از انقباض بتن و ترک های حرارتی دال توصیه می شود که مطابق آن مش حرارتی باید معادل 0.1% از سطح مقطع دال در محل تکیه گاه باشد لیکن EC 4 توصیه میکند مش ضد ترک معادل 0.2% از سطح مقطع دال برای دهانه های دارای شمه بندی باشد.
آنچه در جداول مرجع سریع و نرم افزار طراحی برای مش مشخص شده مطابق ضوابط EC 4 که در نرم افزار میتوان با لغو پیش فرض ها از مقادیر کمتر شبکه آرماتور استغاده نمود.
برای مش A1422(ɸ6mm@200) مقدار همپوشانی300mm برای A193(ɸ7@200mm),A252(ɸ8@200mm), ,A393(ɸ10@200mm)400mm می باشد.
نکته : عدد مشخص شده بعد از A نشانگر مقدار مصرف آرماتور به mm2/m می باشد.
کاهش مش مصرفی
مطابق ضوابط EC 4 مش تقویتی دال باید به طول 1.2m در محل هر تکیه گاه قرار گیرد و در وسط دهانه به شرط آنکه بارهای متمرکز، بازشو و غیره نداشته باشیم، شبکه آرماتور ممکن است نصف شود.
(تا0.2% برای دهانه های با شمع بندی 0.1% دهانه های بدون شمع بندی) لیکن این شبکه باید برای کفایت نرخ آتش سوزی مورد نیاز کنترل شود.
آرماتور تقویت (فولاد تحتانی)
آرماتور تقویت که در محاسبات ظرفیت دال مرکب منظور می گردد میلگردی است که در هر نشیب پروفیل قرار گرفته و فاصله محوری آن به فاصله پایین عرشه تا مرکز میلگرد که در نرم افزار تعریف شده بستگی دارد که حداقل مقدار آن 25mm و حداکثر آن ارتفاع پروفیل می باشد.
آرماتور عرضی
BS Pt4نسبت سطح مقطع آرماتور عرضی بهسطح مقطع بتن بالای پروفیل عرشه را 0.1% مجاز می داند ولی این مسئله در
نرم افزار طراحی در نظر گرفته نمی شود در صورتی که می تواند باعث کاهش بیشتر هزینه ها شود.
چنانچه عرشه به صورت کاملاً پیوسته برروی بال تیر فولادی قرار گرفته یا بصورت متناوب با برشگیرها به تیر فولادی جوش
شده باشد آنگاه به صورت یکپارچه با آرماتور عرضی تیر مرکب عمل می کند.
انتخاب بتن
در قسمت "Concrete Grade" نرم افزار طراحی مقدار مقاومت نمونه مکعبی (به عنوان مثال C30 )وارد می شود.
مقاومت نمونه مکعبی بتن باید مطابق با الزامات دال های مرکب بوده و نباید کمتر از 25MPa وبیشتر از 50MPa باشد.
در طراحی بر اساس EC 4 مقاومت نمونه استوانه ای استفاده می شود. نوع بتن (C25/30) مقاومت نمونه استوانه ای یا مکعبی را
در EC 4 تعریف می کند. بطور کلی مقاومت آزمایشی نمونه استوانه ای 80% مقاومت آزمایشی نمونه مکعبی می باشد.
در نرم افزار طراحی و این بروشور از جدول زیر جهت تبدیل مقادیر مقاومت نمونه استوانه ای و مکعبی استفاده شده است.
دانسیته بتن
در زمان نداشتن اطلاعات جامع و دقیق، فرضیات زیر برای بتن معمولی در نظر گرفته می شود:
بازشو ها
برای ایجاد بازشوها در سقف باید محدوده آنها را قبل از بتن ریزی محصور کرئه و بعد از سخت شدن بتن دال، عرشه را برش زد.
طراحی بازشو ها به اندازه آنها بستگی دارد.
کوچک
بازشوهای تا300mm2 که معمولاً نیاز به تقویت اضافی ندارند.
متوسط
بازشوهای بین300mm2 تا700mm2 که معمولاً به تقویت اضافی در داخل دال نیاز دارند. تقویت دال در زمانی که بازشوها نزدیک به هم باشندنیز باید اعمال گردد.
بزرگ
بازشوهای بزرگتر از 700mm2 که باید با تکیه گاه های دائمی اضافی فولادی، به طور کامل محصور شوند.
قوانین بازشوها
با فرض اینکه d0پهنای بازشوی عمود بر دهانه عرشه باشد.
· فاصله بین بازشو و لبه بدون تکیه گاه باید بزرگتر از 500mm یا d0 باشد. بازشوها نباید از بیشینه مقادیر 1.5d0 (مربوط به بزرگترین بازشو) یا 300mm ،به هم نزدیک تر باشند. در غیر اینصورت باید به عنوان یک بازشو در نظر گرفته شوند.
· سطح کل بازشوهای داخل یک دهانه نباید از کل سطح آن دهانه بیشتر شود.
· طول بازشوی واقع در یک دهانه نباید از طول آن دهانه بیشتر شود.در مواردی که ضوابط فوق اجرا نشوند، بازشوها باید توسط تکیه گاههای دائمی فولادی به طور کامل محصور شوند.
در صورتیکه بازشو در پهنای موثر بال بتنی هر تیر مرکبی قرار بگیرد(بطور معمول 8/1 دهانه از هر سمت محور مرکزی تیر)مقاومت تیر باید با فرض کاهش مناسب پهنای موثر دال، کنترل شود.
طراحی دال اطراف بازشوها
در طراحی دال باید فرض شود که یک سیستم موثر تیرهای نواری، اطراف بازشو را پوشش می دهد.پهنای موثر تیرهای نواری- که به صورت متقاطع با جهت دهانه عرشه عمل می کند-بایدd0/2 در نظر گرفته شود ودر محاسبات فقط تاثیر بتن بالای نشیب های عرشه در نظر گرفته می شود. فرض بر این است که تیرهای نواری عرضی فاصله 1.5d0 را پوشش می دهند. تیرهای نواری طولی بگونه ای طراحی می شوند تا علاوه بر سهم بارهای خود بار ناشی از تیرهای نواری عرضی را هم تحمل نمایند.
فولاد گذاری
آرماتورهای تقویتی در تیرهای نواری، باید متناسب با بارهای وارده، تامین شوند. این آرماتورها معمولاً درون نشیب عرشه قرار می گیرند. علاوه بر این ممکن است آرماتورهای طولی یاعرضی تقویتی برای بهبود انتقال بارهای اطراف بازشو، استفاده می گردد.
طراحی تیر مرکب
وقتی که دال مرکب به طور موثر به تیر فولادی مهار شده باشد آنگاهدر وزن تیر تا 50% صرفه جویی می شود.دال به عنوان یک بال متراکم برای تیر عمل می کند. اتصال بین دال و تیر بوسیله جوش دادن گل میخ های به قطر 19mm و ارتفاع های مختلف متناسب با ارتفاع عرشه فراهم می گردد که بعد از نصب عرشه به تیر جوش داده می شوند. ضخامت بال بالایی مقطع فولادی نباید کمتر از 0.4 برابر قطر گل میخ ها باشد.
(برای مثال 7.6mm برای یک گل میخ19mm).
ظرفیت گل میخ های سرپهن
وقتی که پروفیل عرشه عمود بر تیر فولادی روی بال آن متصل شد، ظرفیت برشی گل میخ های جوش شده طبقجدول ذیل در نظر گرفته می شود. ظرفیت گل میخ ها را می توان با استفاده از فرمول های محاسباتی آیین نامه نیز به دست آورد.
مناسب بودن عرشه های Light deck 60 و Light deck 80
در هر دو عرشه Light deck 60 و Light deck 80، با توجه به موقعیت سخت کننده ها وهم پوشانی در داخل نشیب ها، محل قرار گیری گل میخ ها در مرکز نشیب های عرشه می باشد. این بدین معنی است که گل میخ ها در موقعیت ایده آل خود نصب و ظرفیت بهینه آنها تامین گردیده و نیاز به نظارت کارگاهی در هنگام نصب گل میخ ها به حداقل می رسد.
ارتفاع پروفیل Light deck 80،80mm در نظر گرفته می شود.
گل میخ استاندارد125*19mm (120mm LAW) برای استفاده با Light deck 80 مناسب می باشد.
ارتفاع پروفیل Light deck 60،60mm در نظر گرفته می شود.
گل میخ استاندارد100*19mm (95mm LAW) برای استفاده با Light deck 60 مناسب می باشد.
محدودیت های خیز
در زمان نداشتن اطلاعات مناسب، باید حدود زیر در نظر گرفته شود:
خیز مرحله ساخت
خیز مرحله ساخت فقط به بارهای مرده بدون ضریب بستگی دارد و بارهای زمان ساخت در نظر گرفته نمی شود. حدود خیز برای قالب بندی در قسمت BS 5950.4 ارائه شده است.
دلیل اصلی محدود کردن خیز در مرحله ساخت، محدود کردن حجم بتنی است که بر روی عرشه قرار می گیرد.افزایش خیزها متأثر از افزایش بتن روی عرشه بوده و این امر باعث افزایش بارهای مرده بر سازه می شود.این خیزها به طور معمول نباید از مقادیر زیر بیشتر شوند:
· بدون در نظر گرفتن بتن روی عرشه LP/180
(که نباید از 20mm بیشتر باشد)
· با در نظر گرفتن بتن روی عرشه LP/130
(که نباید از 30mm بیشتر باشد)
LP دهانه موثر قالب بندی است که کمترین مقادیر :فاصله مرکز به مرکز تکیه گاه های دائمی و دهانه خالص بعلاوه ارتفاع پروفیل می باشد.
مطابق BS 5950، وقتی خیز از DS/10 بیشتر می شود- که در آن DS عمق کلی دال مرکب است –وزن بتن اضافی در حین اجرا به دلیل خیز ورقها باید در محاسبات وزن دال مرکب وارد شود. بنابراین در محاسبات خیز قالب بندی در نرم افزار طراحی فقط وقتی که خیز مرحله ساخت از DS/10 بیشتر شود وزن بتن اضافی در محاسبات منظور می گردد.
در نرم افزار طراحی برای ساختمان های بدون شمع بندی خیز مرحله ساخت مجاز L/130، در نظر گرفته شده است که نباید از 30mm بیشتر باشد. تمام جزئیات و پارامترهای محاسبات در راهنمای نرم افزار طراحی آمده است.
دو مقدار برای خیز دال محاسبه می شود(خیز مرحله مرکب):
· خیز ناشی از بارهای اضافی
· خیز کلی
خیز ناشی از بارهای اضافی
LP/350 (که نباید از 20mm بیشتر شود) و آن خیزی است که دال فقط تحت اثر بار های اضافی از خود نشان می دهد.
خیز کل بار
LP/250 (که نباید از 30mm بیشتر شود)
خیز کلی، خیز دال تحت اثر تمام بارهای اعمالی (شامل تمام بارهای مرده ای که بعد از قرار گرفتن دال وارد میشوند مثل وزن کفسازی، تیغه ها و موارد مشابه)بعلاوه خیز مرحله ساخت می باشد. این مقدار در محاسبات اثرات خزش بتن تحت بارهای مرده و هر خیز اضافی که به دلیل تکیه گاه های موقت (شمع بندی ) ایجاد شده وارد می شود.
ارتعاش
نرم افزار طراحی حساسیت دینامیکی دال مرکب را طبق نشریه SCI P076(راهنمای طراحی ارتعاش سقف) کنترل می کند.فرکانس طبیعی تحت اثر وزن دال ، سقف های کاذب، تأسیسات، کفسازی و10% از بارهای اضافی به جای بارهای دائمی وارد بر سقف، محاسبه می شود.
بارها و ترتیب آنها
بارهای ضریب دار در محاسبات وضعیت حد نهایی لحاظ می شوند که با ضرب مقادیر باره در ضریب اطمینان بدست می آید.
بارهای بدون ضریب در وضعیت حد سرویس دهی و شرایط آتش سوزی، در نظر گرفته می شود. این بارها شامکل وزن دال و بارهای زمان ساخت می باشند که بزرگترین مقادیر :150Kpa و 4.5/LP در نظر گرفته می شود. برای دهانه های چند گانه بدن شمع بندی، بار زمان ساخت 1.5/Kpa فقط بر روی یک دهانه در نظر گرفته شده و در سایر دهانه ها نصف این مقدار(0.7Kpa) لحاظ می گردد.
بارهای ساخت بعنوان بارهای اضافی جهت کنترل در نظر گرفته می شوند. بارهای در نظر گرفته شده در مرحله سرویس معمولی شامل وزن دال و بارهای زنده ومرده اضافی می شود.
الزامات اجرای سقف عرشه فولادی
ارتفاع ورق های فولادی ذوزنقه ای در این مقاطع به 75mm محدود می شود.
تامین ضوابط دیافراگم صلب با توجه به ضوابط موجوددر فصل 12آیین نامه ASCE7-05 و ضوابط موجود دراستاندارد2800 ایران الزامی است .
حداکثر تغییر مکان مجاز ناشی از بار مرده حین اجرا به L/180 یا 20 mm برای هر دهانه محدود میشود.
حداکثر تغییر مکان مجازی ناشی از بار زنده بهره برداری به L/360 برای هر دهانه محدود میشود.
رعایت الزامات مربوط به بازشو در سقفها، براساس مبحث نهم مقررات ملی ساختمان الزامی است.
رعایت ضوابط طراحی برشگیرهابراساس بند10-1-2-7 مبحث دهم مقررات ملی ساختمان یا براساس ضوابط موجود در بخش 13 آیین نامه ASCE 7-05 الزامی است.
قطر گل میخهای برش گیر باید 20mm یا کمتر بوده وحداقل ارتفاع آنها بعد از نصب، که از بالای ورق ذوزنقه ای اندازه گیری میشود، نباید کمتر از 40mm باشد.
ضخامت دال بتن آرمه در بالای کنگره ورق ذوزنقه ای نبایداز 50mm کمتر باشد.
رعایت مشخصات فولادهای بکار برده شده بر اساس استاندارد ASTM با حداقل Fy برابر 230MPa الزامی است.
رعایت مشخصات بتن سازه ای برای بتن مورد استفاده در دال بتن ارمه،مطابق با ضوابط موجود در AISC و با حداقل fc برابر 21MPa و حداکثر آن برابر 70MPa وهمچنین رعایت ضوابط مربوط به آرماتور گذاری دال بتن آرمه براساس ضوابط موجود در آیین نامه ACI 318-05 الزامی است.
مقاومت تسلیم آرماتورهای مورد استفاده در دال بتن آرمه رویه، مطابق ضوابط AISC نباید از 525MPa تجاوز کند.
رعایت ضوابط ومقررات مربوط به جوشکاری اعضای سرد نورد شده مطابق استاندارد AISI وآیین نامه های AWS و AISC الزامی است .
رعایت ضوابط راهنمای طراحی Floor vibrations due to human activity منتشر شده توسط انجمن AISC برای کنترل ارتعاش کف ها الزامی است.
رعایت مبحث سوم مقررات ملی ساختمان در خصوص حفاظت ساختمانها در مقابل حریق و همچنین الزامات نشریه شماره 444 مرکز تحقیقات ساختمان ومسکن مربوط به مقاومت جداره ها در مقابل حریق با در نظر گرفتن تعداد طبقات، ابعاد ساختمان،کاربری و وظیفه عملکردی عنصرساختمانی ضروری است.
صدا بندی هوابرد وکوبه ای سقف بین طبقات میبایست مطابق مبحث هجدهم مقررات ملی ساختمان تامین شود.
رعایت الزامات مبحث 19 مقررات ملی ساختمان، جهت صرفه جوئی در مصرف انرژی الزامی است.
در نظر گرفتن جزئیات دقیق مسیر و محل نصب کلیه اجزای تاسیات مکانیکی و برقی در مرحله طراحی و اجرای سقف، ضروری است.
اخذ گواهینامه فنی برای محصول تولیدی، پس از مرکز تحقیقات ساختمان و مسکن الزامی است.
ضوابط جوشکاری گلمیخ در مبحث دهم مقررات ملی ساختمان
ضوابط عمومی
هندسه گلمیخ ها باید برای انجام جوش قوس الکتریکی به وسیله تجهیزات اتوماتیک خاص اینکار مناسب باشد.نوع و اندازه گل میخ باید در نقشه ها مشخصات فنی خصوصی و یا سایر مدارک طراحی تعریف شود.
هر گلمیخ باید دارای یک حلقه محافظ حرارت از جنس سرامیک یا مصالح مناسب دیگر باشد.
ضوابط مکانیکی
گلمیخها باید از جنس میله های سرد کشیده شده باشد.سطح قطعه ای که گلمیخها به آن جوش می شوند باید عاری از هرگونه فلس،زنگ،رطوبت ویا هرهرگونه مواد مضری که مانع از انجام یک جوش مطمئن و خوب می شوند ،باشد. این سطوح ممکن است با برس سیمی سنگ زدن تمیز شوند.
حفاظ قوسی یا حلقه سرامیک حافظ جوشکاری باید بطور کامل خشک باشد.اگر به دلایلی مثل رطوبت موجود در هوا یا اثر باران مرطوب شده باشد باید قبل از استفاده به مدت 2 ساعت در دمای 120 درجه قرار گیرد تا بطور کامل خشک باشد.
فواصل طولی و عرضی برشگیرهای گلمیخ از یکدیگر و همچنین فاصله آنها از لبه بال تیر یا شاهتیر نسبت به آنچه که در نقشه ها نشان داده شده می تواند حداکثر 25 میلیمتر مغایرت داشته باشد. حداقل فاصله لبه پایه گلمیخ از لبه بال تیر مساوی قطر گل میخ بعلاوه 3 میلیمتر است .این فاصله نباید کمتر از 38 میلیمتر باشد.
در مورد گلمیخهایی که در داخل بتن مدفون می شوند حلقه سرامیکی باید شکسته و برداشته شود.در مورد سایر گلمیخها شکستن حلقه سرامیکی اجباری نیست لیکن بهتر است انجام شود.
•
• تکنیک جوشکاری گلمیخ
گلمیخها با استفاده از تجهیزات خودکار جوشکاری گلمیخ دستگاه(Studwelding) که به یک منبع انرژی جریان یکسو با قطبیت مثبت متصل است جوش داده شوند
در حین جوشکاری تفنگی مربوطه باید تا زمان سفت شدن فلزلت مذاب در موقعیت اولیه جوشکاری و بدون حرکت نگاه داشته شود.
در حالتیکه دمای فلز پایه کمتر از 18- می باشد یا سطح جوشکاری مرطوب است باید از انجام جوشکاری پرهیز کرد.
ضوابط ارزیابی گلمیخها
گلمیخهای مورد استفاده در ورقهای ذوزنقه ای آزمایش باید با مصالحی باشد که بیانگر شرایط اجرایی باشند.
· آزمایش خمش
· آزمایش پیچش
· آزمایش کشش
کنترل در حین ساخت
علاوه بر بازرسی عینی آزمایش باید شامل خم کردن گل میخ به انازه تقریبی 30 درجه پس از سرد شدن باشد. آزمایش خم را می توان به کمک یک اهرم و یا ضربات چکش انجام داد.در دمای کمتر از 10 درجه سانتیگراد انجام آزمایش خمش باید با بارگذاری آهسته صورت گیرد تا گل میخ در اثر ترد شکنی از بین نرود.
هنگامیکه یک گلمیخ غیر قابل پذیرش از سطح عضو تحت تنش کششی برداشته می شود سطحی که گلمیخ مورد نظر از آن قسمت حذف شده باید سنگ زده شده و صاف و همسطح گردد.
فرآیندهای جوشکاری
جوشکاری (Welding) فرآیندی صنعتی است که در آن دو ماده (فلزی یا غیر فلزی) را به یکدیگر به روش ذوبی، غیر ذوبی، با فشار یا بدون فشار به وسیله ی ماده ی واسط (پر کننده) یا بدون ماده ی واسط جوش می دهند تا یک اتصال ایجاد شود. در واقع در فرآیند جوشکاری دو یا چند قطعه به هم متصل می شوند و یک عضو پیوسته را تشکیل می دهند.
جوشکاری بر روی طیف وسیعی از فلزات از جمله فولاد، مس، آلومینیوم، برنج و بسیاری دیگر از آلیاژها انجام می شود. مهندسین و جوشکاران با روش های مختلف جوشکاری و با استفاده از طیف گسترده مواد می توانند اتصال ها را با ضخامت، اندازه و شکل مورد نظر اجرا کنند.
جوش ها همانند بست های مکانیکی عمل می کنند و در اتصالات سازه ها جهت انتقال نیرو و انتقال تنش ها از یک عضو سازه به عضو های دیگر استفاده می شوند.
برای ایجاد یک اتصال قوی اغلب از روش ذوب قطعه با مواد واسط (پر کننده) استفاده می شود که به شکل یک حوضچه از مواد مذاب (حوضچه مذاب) می باشد، که پس از انجماد اتصال ایجاد می شود.
قوانین و ضوابط جوشکاری در ساختمان سازی بهوسیله انجمن امریکایی جوشکاری" AWS " به صورت مدون گردآوری شده است. این مجموعه بهصورت آییننامهای در زمینهی جوشکاری در ساخت ساختمانهای فولادی AWS D1.0 و همچنین مشخصات جوشکاری در پلها، بزرگراهها و راه آهن هاAWS D.1.0گردآوری شده است. مشخصات اتصالات جوش شده در ساخت ساختمانهای فلزی درAISC آورده شده است. AISC نیز در مواقع لزوم به استانداردAWS D.1.1 ارجاع میدهد.
فرآیند جوشکاری به دو دسته کلی زیر تقسیم می شود:
فرآیند جوشکاری$welding$
•
در این سری از فرآیند های جوشکاری، هیچ لزومی ندارد که قطعه ذوب شود بلکه فقط می بایست پیوند متالورژیکی بین اجزاء برقرار شود. در حین اتصال درجه حرارت از نقطه ذوب فلزات تجاوز نکرده و هیچگونه آلیاژ پرکن ذوب شونده ( نظیر فرآیند های لحیم گرم و سرد ) بکار گرفته نمی شود. البته این بدان معنا نیست که در حین این فرآیندها هیچ گونه مذابی تشکیل نمی شود، بلکه فاز مذاب مثل یک روانکار عمل می کند. در این فرآیندها برای دستیابی به اتصال با کیفیت بالا بین فلزات اعم از همجنس و غیر همجنس، یا از تغییر فرم و یا از نفوذ و تغییر فرم کمک گرفته می شود.
مزیت جوشکاری حالت جامد
1. هنگامی که حین جوشکاری فلز ذوب می شود، به دلیل انجماد سریع، ساختارهای غیر تعادلی پس از اتصال بوجود می آید. در واقع به دلیل تنش های باقیمانده، ساختار به ترک خوردن حساس می شود. لذا برای اصلاح ساختار باید عملیات حرارتی روی قطعات صورت بگیرد. در جوشکاری حالت جامد، ساختار غیر تعادلی تشکیل نمی شود.
2. وقتی فلز ذوب می شود، میزان انحلال گاز در آن بسیار بالاست. در فرآیندهای ذوبی، سطح مذاب با محیط اطراف کاملاً مواجه شده و امکان جذب گاز وجود دارد. این گازها، میزان حلالیت در جامد را حین انجماد پایین آورده و مذاب یک حالت فوق اشباع پیدا می کند. خروج این گازهای حل شده از بالک جامد قطعه بسیار مشکل و تقریباً غیر ممکن است. گاز هیدروژن بدترین حالت را ایجاد می کند. زیرا به صورت یک ذره پروتون که تحرک آن بسیار بالاست، در مذاب حل می شود. هیدروژن باعث ایجاد ترک سرد یا ترک تأخیری می گردد. در جوشکاری حالت جامد به دلیل عدم وجود مذاب این مشکل نیز دیده نمی شود.
3. در حین جوشکاری انبساط های غیر یکنواخت و در هنگام انجماد انقباض های غیر یکنواخت ایجاد می شود که همراه با ایجاد تنش های کششی می باشد که مستعد ایجاد ترک هستند. لذا در جوشکاری حالت جامد، نوع تنش های باقیمانده در فصل مشترک، تنش های فشاری می باشد که امکان گسترش ترک را از بین می برد.
•
1- جوشکاری اصطکاکی
2-جوشکاری نوردی
3-جوشکاری فشاری
4-جوشکاری انفجاری
5-جوشکاری ضربه ای
6-جوشکاری با فرکانس بالا
7- جوشکاری اصطکاکی – اختلاطی
8-جوشکاری مینیاتوری (التراسونیک)
9- جوشکاری دیفیوژیونی (نفوذی)
اتصال بین دو قطعه فلزی با ذوب کردن لبه ها یا سطح اتصال با یا بدون افزودن فلز پرکننده با یا بدون اعمال فشار را جوشکاری ذوبی می نامند. این نوع فرآیند برای پلاستیک ها و سرامیک ها نیز کاربرد دارد و تحت عنوان جوشکاری امتزاجی شناخته می شود.
کیفیت محصول در این فرآیندها تابع نحوه اجرا می باشد. سه ویژگی خاص در این نوع جوشکاری وجود دارد:
1.شدت منبع حرارتی:
لازمه ذوب کردن قطعه مورد نظر، داشتن یک منبع حرارتی با تمرکز حرارتی است. در جوشکاری، میانگین توان ساطع شده از واحد سطح منبع حرارتی می بایست مد نظر قرار بگیرد. طیف شدت منبع حرارتی مورد استفاده در جوشکاری ذوبی مطابق شکل زیر است:
2.میزان یا نرخ ورود حرارت به قطعه:
میزان انرژی ورودی به قطعه در واحد طول معرف نرخ ورود حرارت است. هر چقدر میزان انرژی بیشتر باشد، دما بالا نمی رود بلکه حجم مذاب تشکیل شده افزایش می یابد. زیرا دما تا نقطه تبخیر فلز بالا رفته و سپس ثابت می شود. پس از آن هدایت حرارتی در قطعه موجب افزایش حجم مذاب می گردد. این افزایش حجم مذاب منجر به افزایش زمان لازم برای انجماد شده و باعث می گردد در سطوح مذاب جذب گازهای اکسیژن، هیدروژن و نیتروژن اتفاق بیفتد. این گازها در قطعه، هم می توانند برخی اکسیدهای ترد ایجاد کرده و یا اینکه به صورت فوق اشباع و حباب گازی تبدیل می شوند. لذا توجه به حرارت ورودی به قطعه و جلوگیری از ایجاد این اشکالات منجر به ارتقای کیفیت جوش می گردد.
•
• 3.نحوه پوشش دادن ناحیه جوش:
در بسیاری از روش های جوشکاری ذوبی، درجه حرارت مذاب بسیار بالا بوده، لذا واکنش پذیری مذاب موجود در حوضچه جوش زیاد است. گازی که در اطراف حوضچه وجود دارد در مذاب حل شده و عیوبی را در منطق جوش ایجاد می کند. لذا لازم است این مناطق به طریقی پوشش داده شون.
انواع پوشش های مورد استفاده در جوشکاری ذوبی به چهار دسته تقسیم می شوند:
فرآیندهای جوشکاری ذوبی بر مبنای منبع تولید حرارت به چهار دسته تقسیم می شوند.
1. منبع حرارتی شیمیایی:
در این روش، یک واکنش شیمیایی موجب تولید حرارت شده (واکنش های گرمازا) و به دو دسته زیر تقسیم می شوند:
1.1. جوشکاری گازی (Oxy Fuel Welding)
2.1. جوشکاری ترمیت (Thermite Welding)
2. منبع حرارتی مقاومتی:
در این روش یک عامل در برابر عبور جریان الکتریکی، مقاومت نشان داده و در اثر آن، حرارت تولید می شود. این جوشکاری نیزی به دسته زیر تقسیم می شود:
1.2. جوشکاری الکترو اسلگ (جوشکاری با سرباره هادی(ESW)
2.2. جوشکاری مقاومتی
3.2. منبع حرارتی قوس:
در این روش، قوس الکتریکی که همان تخلیه الکترونی بین قطب کاتد و آند است، منبع تولید حرارت می باشد.
1.3 جوشکاری با الکترود پوشش دار (SMAW)
2.3. جوشکاری تحت پوشش گازهای محافظ با الکترود تنگستن (GTAW)
3.3. جوشکاری تحت پوشش گازهای محافظ با الکترود مصرفی(GMAW)
4.3. جوشکاری با قوس پلاسما(PAW)
5.3. جوشکاری قوس با الکترود توپودری(FCAW)
6.3. جوشکاری زیر پودری(SAW)
7.3. جوشکاری زائده ای(SW)
8.3. جوشکاری الکترو گس(EGW)
•
4. منبع حرارتی پرتوهای پر انرژی:
در اثر تاباندن این پرتوها بر سطوحی که قرار است بهم جوش شوند، فرآیند ذوب اتفاق می افتد. این نوع جوشکاری شامل طبقه بندی زیر می باشد:
1.4. جوشکاری با پرتو الکترون(EBW)
2.4. جوشکاری با لیزر(LBW)
بایدها ونبایدهای گلمیخ های ساختمانی
گل میخ های برشگیر در یک سازه کامپوزیت نقش بسیار مهم وغیر قابل اغماضی را بعهده دارند "تحمل تنش برشی وانتقال آن" در واقع گل میخ برشگیر مهمترین قطعه در یک سازه کامپوزیت است. استفاده از گل میخ برشگیر غیر استاندارد با توجه به نقش بسیار مهمی که درسازه برعهده دارد از نظر فنی فاجعه و از نظر اخلاقی بسیار نکوهیده می باشد.
این نوشتار سعی دارد ضمن یادآوری استاندارد های تولید وجوشکاری گل میخهای برشگیر با اقتباس از استانداردهای مربوطه وبا تکیه بر الزامات مبحث دهم مقررات ملی ساختمان وآیین نامه جوشکاری ساختمان ایران گامی در جهت اشاعه فرهنگ استفاده از قطعات استاندارد در صنعت ساختمان بردارد،امید است باهمت دست اندرکاران صنعت ساختمان درجهت آگاهی دادن به ناظران، کارفرمایان و مجریان درخصوص استفاده از مصالح استاندارد حافظ جان ومال مردم وحیثیت فنی جامعه مهندسی باشیم.
گل میخ های برشگیر ساختمانی که در سازه های کامپوزیت بطورعام وسقفهای کامپوزیت عرشه فولادی بطور خاص استفاده می شود براساس استاندارد A.W.S- D1.1 که توسط American Welding Society تدوین شده است وهمچنینISO-13918بایستی جوشکاری وتولید شود.
استاندارد تولید درخصوص روش تولید این محصولات جزئیات قابل تاملی را مطرح می کند که مهمترین مواردآن عبارتند از:
•
1. استفاده اجباری از مواد اولیه استاندارد:
متریال مورد استفاده جهت تولید گل میخ های برشگیر بایستی ترکیب شیمیایی خاصی داشته باشد که این مواد را در دسته فولادهای آلیاژی خاص قرار می دهد بنابراین "استفاده از میلگردهای ذوبی جهت تولیدگل میخ به هیچ عنوان مورد تایید نمی باشدوچنین محصولاتی درصورت تولید فاقد ارزش فنی است ضمن اینکه خواص مکانیکی ومقاومت لازم را ندارند".
2. تولید گل میخ استاندارد فقط باروش فورج سرد:
روش تولید گل میخ های برشگیر براساس استاندارد "فورج سرد" عنوان شده است ودلیل فنی آن بهبود خواص مکانیکی قطعات تولیدی است بنابراین "تولید با روش ریخته گری به هیچ عنوان مورد تایید نمی باشدوچنین محصولاتی درصورت تولید فاقد ارزش فنی است ضمن اینکه خواص مکانیکی ومقاومت لازم را نداشته وجوش پذیری مناسب نیزندارند".
3. رعایت کیفیت ابعادی ومشخصات ظاهری:
ابعادتک تک قطعات تولیدی بایستی کاملا مطابق آیین نامه ها کنترل شود ، وجودهرگونه ترک، مویه، لهیدگی، تخلخل وعدم سازگاری ابعادی با نمونه استاندارد نشانه کیفیت پایین قطعه تولیدی بوده و از نظر فنی غیر قابل استفاده شناخته می شود بنابراین "گل میخ های برشگیر که باروشهای ریخته گری،فورج گرم و یا با استفاده از میلگردهای ذوبی تولید می شود به دلیل اینکه ساختار متخلخل و غیر همگن دارند و در فرآیند تولید با کیفیت یکنواخت تولید نمی شوند به هیچ عنوان مورد تایید نمی باشد".
4. به معایب فنی گل میخ های حاصل از ریخته گری و فورج گرم توجه کنید:
· یکسان نبودن استحکام مکانیکی در نواحی مختلف قطعه وسوسه داربودن که سبب ایجادترک ودرنهایت منجربه شکست می شود.
· وجود تنشهای پسماند در قطعات تولیدی به روش ریخته گری و فورج گرم
مقایسه برشگیر گلمیخ در سقف های کامپوزیت عرشه فولادی و برشگیر ناودانی در سقف های کامپوزیت معمولی
سرعت اجرای هر گلمیخ حدود 15 ثانیه می باشد که این زمان برای اجرای برشگیرهای ناودانی در حدود 3 دقیقه می باشد .
برشگیرهای گلمیخ قابلیت انتقال نیروی برش در تمامی جهات را دارا می باشد که این انتقال نیروی برش در برشگیرهای ناودانی فقط محدود به انتقال نیروی برش در جهت طولی ناودانی می باشد .
زمان برقراری قوس الکتریکی در برشگیرهای گلمیخ حدود 800 میلی ثانیه می باشد که این زمان برای اجرای یک برشگیر ناودانی زمانی در حدود 3 دقیقه می باشد .
برشگیرهای گلمیخ عملیات جانبی از قبیل برش کاری و گل زنی جوش را لازم ندارد در حالی که برشگیرهای ناودانی نیاز به برش کاری و گل زنی جوش را دارا می باشد .
کیفیت جوش در برشگیرهای گلمیخ به مراتب بیشتر از کیفیت جوش در برشگیرهای ناودانی می باشد .
اجرای برشگیر گلمیخ به الکترود نیازی نداشته و جوشکاری با استفاده از دستگاه Studwelding انجام می شود .
عدم تغییر شکل تیر فولادی بر اثر حرارت در برشگیرهای استفاده شده از گلمیخ نسبت به برشگیرهای ناودانی.
مقایسه سقف های کامپوزیت عرشه فولادی و کامپوزیت معمولی
در سقف های کامپوزیت عرشه فولادی قالب بندی که یکی از مشکلات اجرایی ساختمان در سقف های کامپوزیت معمولی می باشد،حذف گردیده و اجرای سقف را با سرعت بالا عملی می سازد.
افزایش به لحاظ سادگی اجرا و حذف مراحل قالب بندی
بازگشت سریع سرمایه به لحاظ کاهش زمان اجرا و افزایش سرعت اجرا در سقف های کامپوزیت عرشه فولادی نسبت به سقف های کامپوزیت معمولی
امکان اجرای سقف و بتن ریزی در کلیه طبقات ساختمان به طور هم زمان در سقف های کامپوزیت عرشه فولادی نسبت به سقف های کامپوزیت معمولی
کاهش تعداد تیرهای فرعی در سقف های کامپوزیت عرشه فولادی نسبت به سقف های کامپوزیت معمولی
کاهش هزینه نصب تیرهای فرعی به دلیل کاهش تعداد تیرهای فرعی در سقف های کامپوزیت عرشه فولادی نسبت به سقف های کامپوزیت معمولی
در سقف های کامپوزیت معمولی فاصله بین تیرهای فرعی حدود 90 سانتی متر می باشد که این فاصله در سقف های کامپوزیت عرشه فولادی تا 3 متر بدون استفاده از قالب بندی قابل افزایش می باشد ، که باعث کاهش تعداد تیرهای فرعی در سقف های کامپوزیت عرشه فولادی نسبت به سقف های کامپوزیت معمولی می شود .
ضخامت بتن در سقف های کامپوزیت عرشه فولادی به دلیل فرم عرشه به مراتب کمتر از ضخامت بتن در سقف های کامپوزیت معمولی می باشد و به طور متوسط 2 سانتی متر کمتر می باشد .
کاهش وزن سقف در حدود 50 کیلوگرم بر متر مربع در سقف های کامپوزیت عرشه فولادی نسبت به سقف های کامپوزیت معمولی.
کاهش آرماتور مورد نیاز در سقفهای کامپوزیت عرشه فولادی نسبت به سقف ها ی کامپوزیت معمولی با کم شدن وزن سقف به دلیل کاهش تعداد تیرهای فرعی و ضخامت بتن وزن کل سازه کاهش یافته که باعث اقتصادی تر شدن طراحی و محاسبات مربوطه می شود .
• با کم شدن وزن سازه در ساختمانهای ساخته شده با سقف کامپوزیت عرشه فولادی نسبت به ساختمانهای کامپوزیت معمولی ، این ساختمانها نیروی کمتری از زلزله را به خود گرفته و باعث کاهش صدمات وارده بر ساختمان در زلزله می شود .
• تثبیت عرشه بر روی تیرریزی
• قسمت پایین عرشه باید بلافاصله بعد از نصب آن روی روی تکیه گاه های سازه تثبیت شود. برای این منظور از میخ پرچ یا میخ های سرمته استفاده می شود. در مکان هایی که گل میخ نصب می شود، هر ورق عرشه نیاز به دو تثبیت کننده در تکیه گاه انتهایی و یک تثبیت کننده در تکیه گاه های میانی دارد.
•
• الزامات تکیه گاهی
•
• برشگیرها
• o برشگیرها معمولاً گل میخ های سرپهن با ضخامت 19mm می باشند که برروی تیرهای تکیه گاهی در سراسر عرشه جوش داده می شوند، این مرحله توسط متخصصین جوشکاری گل میخ و با دستگاه مخصوص stud welding اجرا می شود.
شرایط کارگاه باید برای جوشکاری و آزمایش های خمش که به طور مقتضی انجام میشود، مناسب باشد. فاصله وموقعیت برشگیر ها حائض اهمیت بوده و باید توسط مهندس طراح بر روی نقشه های اجرایی عرشه ها تعریف شود.
o حداقل فاصله گذاری:حداقل فاصله گل میخ ها در امتداد تیر باید 6d و در عرض تیر 4dباشد، که d قطر اسمی گل میخ است.
o در جایی که ردیف گل میخ بصورت زیگ زاگ است، حداقل فاصله عرضی گل میخ ها باید 3d باشد.
o حداکثر فاصله: در نواحی از عضو مرکب که در معرض اثرات غیر الاستیک زلزله قرار ندارندحداکثر فاصله800mm و در نواحی که در معرض اثرات غیر الاستیک زلزله قرار دارند(نواحی تسلیم)حداکثر فاصله 400mm می باشد.
•o گل میخ نباید نزدیک تر از 25mm به لبه تیر باشد.
راهنمایی های بیشتر در مورد برشگیرها برای طراحان و نصابان در فصل هفتم نشریه 288(آیین نامه جوشکاری ساختمانی ایران) و در مبحث دهم مقررات ملی ساختمان موجود است.
•
قرار گیری مش
اصولاً مش استاندارد، مانندA192 ,A193 ,A142در نزدیک بالای دال مورد نیاز است. پوشش بالای مش تقویتی باید توسط مهندس طراح مشخص شده و از اسپیسر برای حفظ ارتفاع صحیح استفاده گردد.برای همپوشانی مش 300mm,A142و برای مش های 400mm,A393, A252 ,A193 را باید در نظر گرفت.
•بتن ریزی
قبل از ریختن بتن باید سطح عرشه از هرگونه خاک وروغن که می تواند تأثیر مخالف بر دال سخت شده داشته باشد،زدوده شود. بتن باید بصورت هموار ریخته شود تا بار را در امتداد هر ورق توزیع نماید.
جهت جلوگیری از انباشته شدن بتن در سطح باید مراقبت لازم به عمل آید.
بازشوها
اطراف بازشوهای با ابعاد 300mm2 تا 700mm2 باید توسط میلگرد تقویت شوند. بازشوها باید قبل از بتن ریزی محصور و بعد از سخت شدن بتن عرشه بریده شود.
در بازشوهای بزرگتر باید محیط بازشو با پروفیل فولادی محصور گردد، فولادها باید از قبل بر روی عرشه نصب شود. توجه: بازشو درون عرشه فولادی قبل از بتن ریزی یا بل از سخت شدن بتن نباید بریده شود.
•
تکیه گاه های موقت
برای مهار موقت عرشه باید از تیرهای چوبی که بر روی تکیه گاه های موقت با فواصل مرکزی یک متر نگهداری شده، استفاده شود.
· تیر های چوبی وشمع ها باید دارای مقاومت مناسب باشند.
· تکیه گاه های موقت در وسط دهانه قرار می گیرند و در صورت نیاز به تکیه گاه های بیشتر در دهانه، آنها را در محل های مناسب با هماهنگی مهندس طراح قرار می دهند.
· حداقل پهنای تیرهای توزیع بار یا تیر های چوبی 100mm و حداکثر انحراف 10mmمی باشد و باید لبه باریک آنها در بالا قرار بگیرد.
· سازه تکیه گاهی نباید تا زمانی کهخ بتن به 70% مقاومت مشخصه خود نرسبده برداشته شود.
•
نکات ایمنی کلیاز تکنیک های مفید که به صورت خلاصه در زیر آورده شده که در نشریات SCI انگلستان آمده باید پیروی نمود. همیشه عرشه را قبل از استفاده به عنوان سکوی کار مطمئن ثببیت نمایید.
· همه اقدامات امنیتی شخصی از جمله استفاده از کلاه های سفت و لباسهای حفاظتی صورت گیرد.
· همه اقدامات امنیتی کارگاه از جمله خطوط ایمنی، حفاظت لبه ها و مهار مناسب نردبان ها صورت پذیرد.
· هیچ ورق عرشه ای تثبیت نشده رها نشود.
· بتن توده نشده و از ارتفاع رها نشود.
· بار های سنگین بر روی عرشه حفاظت نشده قرار نگیرد.
· تکیه گاه های موفت بر روی بتن سخت نشده قرار نگیرد
· سوراخ ها و حفره های بر روی عرشه قبل از بتن ریزی بریده نشوند.
راهنمای طراحی داده شده در این برشور و نرم افزار طراحی مطابق با استاندارد های زیر است.
استاندارد های انگلیسی
· عرشه سقف مرکب
1. BS 5950 : قسمت 4 . کاربرد سازه ایی فولاد در ساختمان: دستور العمل عمومی طراحی دالهای مرکب با پروفیل عرشه های فولادی
· تیر های فولادی مرکب
2. BS 5950 : قسمت3 . طراحی در ساختمانهای مرکب :بخش 1-3 دستورالعمل عمومی برای طراحی تیر های مرکب ساده و پیوسته.
· پروفیل عرشه فولادی
3. BS 5950 : قسمت 6 . کاربرد سازه ای فولاد در ساختمان. : دستور العمل عمومی طراحی نمونه سبک پروفیل عرشه های فولادی.
· مقاومت در برابر آتش
4. BS 5950 : قسمت 8 . کاربرد سازه ای فولاد در ساختمان. : دستور العمل عمومی طراحی برای مقاومت در برابر آتش.
· بتن
5. BS 8110 : قسمت 1 . کاربرد سازه ای بتن : دستور العمل عمومی برای طراحی و ساخت.
6. BS 8110 : قسمت 2 . کاربرد سازه ای بتن : دستور العمل عمومی برای رویداد های خاص.
· آرماتور ها
7. BS 4483 : مشخصات تولید فولاد برای تقویت بتن .
8. BS 4483 : مشخصات میلگرد های فولادی برای تقویت بتن .
· Eurocode 4
9. ENV 1993 : طراحی سازه ای فولادی: قوانین تکمیلی برای ورق ها و اعضای باریک نورد سرد شده
10. ENV 1994 : طراحی سازه های مرکب فولادی و بتنی.قوانین کلی برای ساخت
11. ENV 1994 : طراحی سازه های مرکب فولادی و بتنی. طراحی سازه ای در برابر آتش سوزی.
12. SCI-P-076: راهنمای طراحی برای ارتعاش سقف ها مطابق با CIRIA)1989)
نکات طراحی
1- حدود استفاده شده در جدول ممکن است مناسب پروژه شما نباشد. لطفاً برای اطلاع از مسائل مربوط به پروژه خود به طور مستقیم با فرابهین تماس حاصل فرمایید.
2- برای دستیابی به دهانه های بزرگ تر می توان از دو ردیف تکیه گاههای موقت (شمع بندی) و یا تیرهای عریض تر استفاده نمود.
3- دهانه های نشان داده شده در جدول فقط بعنوان نمونه بوده و توصیه می گردد جهت طراحی خاص از مشاوره گروه پشتیبانی شرکت فرابهین استفاده گردد.
•
پارامترهای طراحی
عرشه سقف مرکب عموماً با توجه به شرایط مرحله ساخت، بار ودهانه مورد نیاز برای سرویس دهی و مقاومت در برابر آتش سوزی فراهم می شود.
نرخ آتش سوزی
مقاومت= تعیین اندازه شبکه یا فولاد مورد استفاده زیرین
• عایق بودن= تعیین حداقل عمق دال
• از آنجا که عرشه همانند یک پوسته رفتار می نماید یکپارچگی همواره فراهم می باشد.
• خواص صوتی ساختمان
• با در نظر گرفتن مقدار ضخامت دال نرخ عایق بودن در برابر صوت انتخاب می شود.
• ارتعاش
• متناسب با دهانه به ضخامت دال همانند وضعیت تیرهای تکیه کاهی در طراحی ارتعاش موثر است.
• وزن بتن
• وزن بتن، حداقل عمق دال و دهانه را در زمان بتن ریزی تحت تأثیر قرار می دهد.
دهانه عرشه (بدون شمع بندی)
اندازه تیر و فاصله تیر ها از هم، دهانه عرشه را تعیین می نماید.
دهانه عرشه (دارای شمع بندی)
برای استفاده کامل از خواص دال مرکب ممکن است نیاز به شمع بندی موقت باشد.
طراحی دو مرحله ای
همه سقف های مرکب باید در دو مرحله در نظر گرفته شوند.
1-بتن مرطوب/مرحله ساخت
o بار به تنهایی توسط عرشه تحمل می شود.
o خیزها ناشی از بار بتن، بتن روی عرشه و بارهای ساخت می باشد.
o خیز کلی سیستم ناشی از خیز تیرها می باشد.
2-بتن سخت شده/مرحله مرکب
o بار توسط دال مرکب تحمل می شود.
o خیزها ناشی از تغییر مکان تکیه گاههای موقت (شمع بندی) در صورت وجود، بارهای اضافی و خیز تیرها در نظر گرفته می شود.
هدف کلی طراحی
معمولاً طراحان ترجیح می دهند تا نیاز به شمع بندی موقت را کاهش دهند در نتیجه دهانه و عمق مورد نیاز دال در انتخاب عرشه کنترل کننده می باشد.
معمولاً الزامات آتش سوزی تعیین کننده عمق دال می باشند و برای بیشتر حالتهای بدون شمع بندی، بارهای اضافی روی دال طراحی را محدود نمی کند.
مش ضد ترک (آرماتور حرارتی)
جهت کاهش ترک های ناشی از لنگر خمشی موجود در سقف آرماتورهای تقویتی مورد نیاز بر روی تیرهای تکیه گاهی تعبیه می شوند.
قوانین(BS Pt4) به عنوان معتبرترین ضوابط کنترل ترک های ناشی از انقباض بتن و ترک های حرارتی دال توصیه می شود که مطابق آن مش حرارتی باید معادل 0.1% از سطح مقطع دال در محل تکیه گاه باشد. لیکن EC 4 توصیه می کند مش ضد ترک معادل 0.2% از سطح مقطع دال برای دهانه های دارای شمع بندی باشد
آنچه در جداول مرجع سریع و نرم افزار طراحی برای مش مشخص شده مطابق ضوابط EC 4 که در نرم افزار میتوان با لغو پیش فرض ها از مقادیر کمتر شبکه آرماتور استفاده نمود. برای مش A142 (ɸ6mm@200) مقدار همپوشانی 300mm برای 400mm می باشد.
نکته: عدد مشخص شده بعد از A نشانگر مقدار مصرف آرماتور به mm2/m می باشد.
کاهش مش مصرفی
مطابق ضوابط EC 4 مش تقویتی دال باید به طول 1.2m در محل هر تکیه گاه قرار گیرد و در وسط دهانه به شرط آنکه بارهای متمرکز، بازشو و غیره نداشته باشیم، شبکه آرماتور ممکن است نصف شود.
(تا0.2% برای دهانه های با شمع بندی 0.1% دهانه های بدون شمع بندی) لیکن این شبکه باید برای کفایت نرخ آتش سوزی مورد نیاز کنترل شود.
آرماتور تقویت (فولاد تحتانی)
آرماتور تقویت که در محاسبات ظرفیت دال مرکب منظور می گردد میلگردی است که در هر نشیب پروفیل قرار گرفته و فاصله محوری آن به فاصله پایین عرشه تا مرکز میلگرد که در نرم افزار تعریف شده بستگی دارد که حداقل مقدار آن 25mm و حداکثر آن ارتفاع پروفیل می باشد.
آرماتور عرضی
BS Pt4نسبت سطح مقطع آرماتور عرضی بهسطح مقطع بتن بالای پروفیل عرشه را 0.1% مجاز می داند ولی این مسئله در نرم افزار طراحی در نظر گرفته نمی شود در صورتی که می تواند باعث کاهش بیشتر هزینه ها شود.
چنانچه عرشه به صورت کاملاً پیوسته برروی بال تیر فولادی قرار گرفته یا بصورت متناوب با برشگیرها به تیر فولادی جوش شده باشد آنگاه به صورت یکپارچه با آرماتور عرضی تیر مرکب عمل می کند.
انتخاب بتن
در قسمت "Concrete Grade" نرم افزار طراحی مقدار مقاومت نمونه مکعبی (به عنوان مثال C30)وارد می شود.
مقاومت نمونه مکعبی بتن باید مطابق با الزامات دال های مرکب بوده و نباید کمتر از 25MPaوبیشتر از 50MPa باشد.
در طراحی بر اساس EC 4 مقاومت نمونه استوانه ای استفاده می شود. نوع بتن (C25/30) مقاومت نمونه استوانه ای یا مکعبی را در EC 4 تعریف می کند. بطور کلی مقاومت آزمایشی نمونه استوانه ای 80% مقاومت آزمایشی نمونه مکعبی می باشد.
در نرم افزار طراحی و این بروشور از جدول زیر جهت تبدیل مقادیر مقاومت نمونه استوانه ای و مکعبی استفاده شده است.
دانسیته بتن
در زمان نداشتن اطلاعات جامع و دقیق، فرضیات زیر برای بتن معمولی در نظر گرفته می شود:
بازشو ها
برای ایجاد بازشوها در سقف باید محدوده آنها را قبل از بتن ریزی محصور کرئه و بعد از سخت شدن بتن دال، عرشه را برش زد.
طراحی بازشو ها به اندازه آنها بستگی دارد.
کوچک
بازشوهای تا300mm2 که معمولاً نیاز به تقویت اضافی ندارند.
متوسط
بازشوهای بین300mm2 تا700mm2 که معمولاً به تقویت اضافی در داخل دال نیاز دارند. تقویت دال در زمانی که بازشوها نزدیک به هم باشندنیز باید اعمال گردد.
بزرگ
بازشوهای بزرگتر از 700mm2که باید با تکیه گاه های دائمی اضافی فولادی، به طور کامل محصور شوند.
قوانین بازشوها
با فرض اینکه d0پهنای بازشوی عمود بر دهانه عرشه باشد.
·فاصله بین بازشو و لبه بدون تکیه گاه باید بزرگتر از 500mmیا d0باشد. بازشوها نباید از بیشینه مقادیر 1.5d0 (مربوط به بزرگترین بازشو) یا 300mm،به هم نزدیک تر باشند. در غیر اینصورت باید به عنوان یک بازشو در نظر گرفته شوند.
·سطح کل بازشوهای داخل یک دهانه نباید از کل سطح آن دهانه بیشتر شود.
·طول بازشوی واقع در یک دهانه نباید از طول آن دهانه بیشتر شود.در مواردی که ضوابط فوق اجرا نشوند، بازشوها باید توسط تکیه گاههای دائمی فولادی به طور کامل محصور شوند.
در صورتیکه بازشو در پهنای موثر بال بتنی هر تیر مرکبی قرار بگیرد(بطور معمول 8/1 دهانه از هر سمت محور مرکزی تیر)مقاومت تیر باید با فرض کاهش مناسب پهنای موثر دال، کنترل شود.
طراحی دال اطراف بازشوها
در طراحی دال باید فرض شود که یک سیستم موثر تیرهای نواری، اطراف بازشو را پوشش می دهد.پهنای موثر تیرهای نواری- که به صورت متقاطع با جهت دهانه عرشه عمل می کند-بایدd0/2 در نظر گرفته شود ودر محاسبات فقط تاثیر بتن بالای نشیب های عرشه در نظر گرفته می شود. فرض بر این است که تیرهای نواری عرضی فاصله 1.5d0 را پوشش می دهند. تیرهای نواری طولی بگونه ای طراحی می شوند تا علاوه بر سهم بارهای خود بار ناشی از تیرهای نواری عرضی را هم تحمل نمایند.
فولاد گذاری
آرماتورهای تقویتی در تیرهای نواری، باید متناسب با بارهای وارده، تامین شوند. این آرماتورها معمولاً درون نشیب عرشه قرار می گیرند. علاوه بر این ممکن است آرماتورهای طولی یاعرضی تقویتی برای بهبود انتقال بارهای اطراف بازشو، استفاده می گردد.
طراحی تیر مرکب
وقتی که دال مرکب به طور موثر به تیر فولادی مهار شده باشد آنگاه در وزن تیر تا 50% صرفه جویی می شود.دال به عنوان یک بال متراکم برای تیر عمل می کند. اتصال بین دال و تیر بوسیله جوش دادن گل میخ های به قطر 19mm و ارتفاع های مختلف متناسب با ارتفاع عرشه فراهم می گردد که بعد از نصب عرشه به تیر جوش داده می شوند. ضخامت بال بالایی مقطع فولادی نباید کمتر از 0.4 برابر قطر گل میخ ها باشد.
(برای مثال 7.6mm برای یک گل میخ19mm).
ظرفیت گل میخ های سرپهن
وقتی که پروفیل عرشه عمود بر تیر فولادی روی بال آن متصل شد، ظرفیت برشی گل میخ های جوش شده طبقجدول ذیل در نظر گرفته می شود. ظرفیت گل میخ ها را می توان با استفاده از فرمول های محاسباتی آیین نامه نیز به دست آورد.
در عرشه LightDeck 60، با توجه به موقعیت سخت کننده ها وهم پوشانی در داخل نشیب ها، محل قرار گیری گل میخ ها در مرکز عرشه می باشد. این بدین معنی است که گل میخ ها در موقعیت ایده آل خود نصب و ظرفیت بهینه آنها تامین گردیده و نیاز به نظارت کارگاهی در هنگام نصب گل میخ ها به حداقل می رسد.
ارتفاع پروفیل LightDeck 60،60mm در نظر گرفته می شود.
گل میخ استاندارد100*19mm (95mm LAW) برای استفاده با LightDeck 60 مناسب می باشد.
مقاومت در برابر آتش سوزی
ضوابط فصل 8، BS 5950 مربوط به الزامات مقاومت در برابر آتش سوزی باید رعایت گردیده و در محاسبات جداول و نرم افزار وارد شوند.
برشگیر ها در شرایط آتش سوزی
چنانچه مرکب بودن تیر فولادی با دال بتنی روی آن توسط برشگیر ها به میزان کافی فراهم شود آنگاه در زمان طراحی تیر فولادی در برابر آتش سوزی میتوان از وزن دال صرفنظر نمود.
روش های طراحی در برابر آتش سوزی
سه شرط برای طراحی در برابر آتش سوزی وجود دارد:
·مقاومت خمشی در شرایط آتش سوزی
·حداقل عمق دال جهت میزان عایق بودن
·یکپارچگی دال برای محافظت در برابر آتش
ظرفیت دال مرکب در آتش سوزی میتواند با استفاده از روش ساده یا روش طراحی در برابر آتش سوزی بر اساس Eurocodes، محاسبه شود که روش ساده، اقتصادی تر است.
روش ساده
امکان استفاده از روش ساده برای عرشه های تقویت شده و عرشه هایی که بر روی یک تکیه گاه داخلی یا بیشتر که به صورت پیوسته ادامه می یابند، وجود دارد. در این روش تخمین مقاومت در آتش سوزی بر اساس یک یا دو شبکه مش استاندارد می باشد و از هرگونه آرماتور تقویت صرفنظر می گردد.
روش طراحی در برابر آتش سوزی
روش طراحی در برابر آتش سوزی کاربرد کلی دارد.تخمین مقاومت در برابر آتش سوزی بر اساس یک یا دو شبکه مش استاندارد در بالا و یک میلگرد درهرنشیب عرشه می باشد.
•
.محدودیت های خیز
در زمان نداشتن اطلاعات مناسب، باید حدود زیر در نظر گرفته شود:
خیز مرحله ساخت
خیز مرحله ساخت فقط به بارهای مرده بدون ضریب بستگی دارد و بارهای زمان ساخت در نظر گرفته نمی شود. حدود خیز برای قالب بندی در قسمت BS 5950.4 ارائه شده است.
دلیل اصلی محدود کردن خیز در مرحله ساخت، محدود کردن حجم بتنی است که بر روی عرشه قرار می گیرد.افزایش خیزها متأثر از افزایش بتن روی عرشه بوده و این امر باعث افزایش بارهای مرده بر سازه می شود.این خیزها به طور معمول نباید از مقادیر زیر بیشتر شوند:
·بدون در نظر گرفتن بتن روی عرشه LP/180
(که نباید از 20mmبیشتر باشد)
·با در نظر گرفتن بتن روی عرشه LP/130
(که نباید از 30mmبیشتر باشد)
LPدهانه موثر قالب بندی است که کمترین مقادیر :فاصله مرکز به مرکز تکیه گاه های دائمی و دهانه خالص بعلاوه ارتفاع پروفیل می باشد.
مطابق BS 5950، وقتی خیز از DS/10بیشتر می شود- که در آن DS عمق کلی دال مرکب است –وزن بتن اضافی در حین اجرا به دلیل خیز ورقها باید در محاسبات وزن دال مرکب وارد شود. بنابراین در محاسبات خیز قالب بندی در نرم افزار طراحی فقط وقتی که خیز مرحله ساخت از DS/10 بیشتر شود وزن بتن اضافی در محاسبات منظور می گردد.
در نرم افزار طراحی برای ساختمان های بدون شمع بندی خیز مرحله ساخت مجاز L/130، در نظر گرفته شده است که نباید از 30mmبیشتر باشد.
•
دو مقدار برای خیز دال محاسبه می شود(خیز مرحله مرکب):
·خیز ناشی از بارهای اضافی
·خیز کلی
خیز ناشی از بارهای اضافی
• LP/350(که نباید از 20mmبیشتر شود) و آن خیزی است که دال فقط تحت اثر بار های اضافی از خود نشان می دهد.
• خیز کل بار
• LP/250 (که نباید از 30mmبیشتر شود)
• خیز کلی، خیز دال تحت اثر تمام بارهای اعمالی (شامل تمام بارهای مرده ای که بعد از قرار گرفتن دال وارد میشوند مثل وزن کفسازی، تیغه ها و موارد مشابه)بعلاوه خیز مرحله ساخت می باشد. این مقدار در محاسبات اثرات خزش بتن تحت بارهای مرده و هر خیز اضافی که به دلیل تکیه گاه های موقت (شمع بندی) ایجاد شده وارد می شود.
•
• ارتعاش
• نرم افزار طراحی حساسیت دینامیکی دال مرکب را طبق نشریه SCI P354(راهنمای طراحی ارتعاش سقف) کنترل می کند.فرکانس طبیعی تحت اثر وزن دال ، سقف های کاذب، تأسیسات، کفسازی و10% از بارهای اضافی به جای بارهای دائمی وارد بر سقف، محاسبه می شود.
•
• بارها و ترتیب آنها
• بارهای ضریب دار در محاسبات وضعیت حد نهایی لحاظ می شوند که با ضرب مقادیر باره در ضریب اطمینان بدست می آید.
• بارهای بدون ضریب در وضعیت حد سرویس دهی و شرایط آتش سوزی، در نظر گرفته می شود. این بارها شامکل وزن دال و بارهای زمان ساخت می باشند که بزرگترین مقادیر:150Kpa و 4.5/LPدر نظر گرفته می شود. برای دهانه های چند گانه بدن شمع بندی، بار زمان ساخت 1.5/Kpa فقط بر روی یک دهانه در نظر گرفته شده و در سایر دهانه ها نصف این مقدار(0.7Kpa) لحاظ می گردد.
• بارهای ساخت بعنوان بارهای اضافی جهت کنترل در نظر گرفته می شوند. بارهای در نظر گرفته شده در مرحله سرویس معمولی شامل وزن دال و بارهای زنده ومرده اضافی می شود.
•
سقف عرشه فولادي
پیمانکاری در سراسر ایران
همراه کادر مجرب و متخصصین
در این روش سقف عرشه فولادي
اجرای سقف از ورق های فولادی فرم داده شده استفاده میشود.
اجراء کلی تشکیل دهنده این سقف عبارتند از:
1. ورقهای فولادی پروفیل شده
3. میلگرد آرماتور یا مش بندی
4. بتن
روش کار به این صورت است که پس از آماده شدن سازه جهت اجرای سقف
اندازه هر دهانه گرفته شده و براساس طول دهانه سقف و بارگذاری محاسبه شده
مربوطه ورق های لازم در کارخانه فرم داده می شود و برش می خورد.
ورق ها پس از انتقال به محل اجرای سقف بر روی دهانه مربوطه روی سازه
قرار میگیرد. در مرحله بعد برش گیر یا گل میخ ها با استفاده از میخ کوب تفنگی
به سازه پرچ شده و یا با استفاده از دستگاه جوش به سازه جوشکاری میشود.
بعداز آن میلگردهای افت حرارت و یا مش بندی آماده بر روی ورق ها نصب
و آماده بتن ریزی میشود. این نوع سقف را میتوان درحالت کلی با دهانه
بیش از 2.5 متر را با یک تیر فرعی اجرا نمود.
مزایای سقف عرشه فولادی:
1. وزن پایین
2. سرعت بالا در اجرا
3. نصب سریع و راحت
4. عدم نیاز به شمع بندی
5. امکان بتن ریزی چندین سقف همزمان
6.مصرف پایین بتن
7. وزن و هزینه اجرای آن حداقل به میزان 10 تا 40 درصد کمتر از
سقف های معمول می باشد.
8. عملکرد مرکب سقف باعث کاهش وزن اسکلت می گردد.
9. امکان افزایش فاصله تیرها تا 3/5 متر بدون نیاز به شمع بندی وجود دارد.
10. در این نوع سقف قالب بندی حذف شده و ورقهای عرشه در حین اجرا
به عنوان قالب عمل میکنند.
11. نیازی به آرماتور کششی در این سقف نبوده و ورقهای عرشه پس از
گیرش بتن به عنوان فولاد کششی عمل خواهند کرد.
کناره ها و بازشوها
بازشوها ( Slab Openings )
در سقف های مرکب عرشه فولادی به
سه دسته زیر تقسیم می شوند:
بازشوهای کوچک که ابعاد آنها کمتر از 300 میلیمتر بوده
و به طور معمول نیازی یه تقویت اضافی در دور آنها وجود ندارد.
بازشوهای متوسط که ابعاد آنها بین 300 و 700 میلیمتر بوده
و بایستی میلگرد تقویتی در دور آنها اجرا نمود.
بازشوهای بزرگ که ابعاد آنها بیشتر از 700 میلیمتر بوده
و در این حالت با تیرریزی مناسب در دور آنها بایستی
ایستائی لازم را ایجاد نمود.
قسمتهای طره ( Cantilevers )
طول طره سقف ها نبایستی بیشتر از 600 میلیمتر باشد
در غیر اینصورت باید از شمع های موقت در حین اجرا
همچنین آرماتور اضافه منفی استفاده نمود.
حداکثر طول طره در حالتی که تیرها موازی
ورق های عرشه هستند 200 میلیمتر می باشد.
حدود بارگذاری
تغییر مکان
ارتعاش
بارهای حین اجرا ( Construction Loads )
بارهای حین اجرا شامل وزن بتن در حالت خیس و وزن
عرشه به اضافه بار اجرا برابر 150 کیلوگرم
بر مترمربع می باشد.
بارگذاری کامل ( Total Load )
بارگذاری کامل شامل وزن بتن در حالت خشک،
ورق عرشه، پارتیشن، سقف کاذب،
مصالح پرکننده کف و بار زنده طبقه میباشد.
تغییرمکان سقف مرکب (Steel Deck Deflection)
تغییرمکان سقف پس از گیرش نهایی بتن
و اطمینان از عملکرد مرکب سقف نبایستی
از مقادیر زیر تجاوز نماید:
حداقل Lp/350 و 20 میلیمتر برای بارهای
مرده اضافه (Super Dead Load) و بار زنده
Lp/250 برای بارگذاری کامل
تغییر مکان ورق عرشه (Steel Deck Deflection)
تغییر مکان ورق عرشه در حین اجرا نبایستی از
مقادیر زیر تجاوز نماید:
Lp/180حداقل و 20 میلیمتر برای بارهای حین اجرا
در صورتی که اثر انباشتگی بتن منظور نشده باشد.
Lp/130حداقل و 30 میلیمتر برای بارهای حین اجرا
در صورتی که اثر انباشتگی بتن منظور شده باشد.
که در آن Lp برابر طول خالص دهانه ورق عرشه میباشد.
ارتعاش سقف ( Floor Vibration )
فرکانس طبیعی تمام سقف ها با احتساب
بارهای مرده،تاسیسات، سقف کاذب، به اضافه
10 درصد از بار زنده محاسبه میگردد.
در سقف های با کاربری های اداری و مسکونی
این فرکانس نبایستی کمتر از 5 هرتز باشد
و در سقف های با کاربری ورزشی،
آمفی تئاترها وتکیه گاه ماشین آلات این
حد مجاز براساس توصیه استانداردهای
SCI-P076,P354 بایستی افزایش یابد.
مبانی طراحی
طراحی سقف های مرکب عرشه فولادی بر اساس
استاندارد BS به شرح عناوین زیر انجام میشود:
BS5950-Part 4 Code of practice for design of composite slabs with profiled steel sheeting
BS5950-Part 6 Code of practice for design of light gauge profiled steel sheeting
BS5950-Part 8 Code of practice for fire resistant design
BS5950-Part 9 Code of practice forstressed skin design
هدف از طراحی انتخاب بهترین مقطع ورق عرشه
طوریکه علاوه بر داشتن حداقل وزن و حداکثر باربری،
موجب کاهش حجم بتن نیز گردد. و این طراحی
به سه مرحله زیر قابل تفکیک میباشد:
1. طراحی در حین اجرا
2. طراحی مرکب سقف پس از گیرش نهایی بتن
3. طراحی در برابر آتش
در صورت عدم استفاده از شمع گذاری موقت،
در بیشتر حالات شرایط حین اجرا حاکم بر طرح ورق
عرشه بوده و ضخامت بتن سقف نیز بر اساس نیاز
مهندسی درملاحظات تغییرمکان،مقاومت دربرابر آتش،
لرزش و صداگیری سقف تعیین میگردد.
خصوصیات ورق عرشه
(Deck Material Specification)
ورقهای عرشه از ورقهای گالوانیزه منطبق با
استاندارد BS1449-G43/25 با حداقل مقاومت
جاری شدن 2500 کیلوگرم بر سانتیمتر مربع
ساخته میشوند که وزن لایه روی Zn در دو ظرف
آن برابر 275 گرم بر مترمربع و با ضخامت
تقریبی 0/04 میلیمتر میباشد.
مشخصات بتن (Concrete Specification)
بتن سقف از رده C30 بر اساس استاندارد BS8110
با مقاومت مشخصه فشاری 300 کیلوگرم بر
سانتیمتر مربع برای نمونه مکعبی با قطر سنگدانه
20 میلیمتر فرض شده است. جرم حجمی این بتن
در شرایط خیس و خشک به شرح زیر است:
Concrete density in wet &dry cases, kg/m3
Modular Ratio Dry Wet Concrete Type
10 2400 2500 بتن معمولی NWC
15 1800 1900 بتن سبک LWC
شمع گذاری موقت ( Temporary Propping )
اولین انتخاب در طراحی این نوع سقف ها
اجرای آن بدون نیاز به شمع گذاری موقت
یباشد. اما در صورت لزوم معمولا از یک
ردیف شمع با عرض نشیمن حداقل
100 میلیمتر در وسط دهانه کفایت میکند.
این شمع ها تا زمان رسیدن مقاومت بتن
به 75 درصد مقاومت نهایی
آن نبایستی جابجا گردند.
تامین تکیه گاه جانبی برای تیرها
(Deck Providing Full Lateral Restraint )
ورق های عرشه با توجه به تثبیت مناسب
بر روی تیرها تکیه گاه جانبی برای بال
فشاری تیرهای ساده محسوب شده
و طراح سازه میتواند بدون کاهش در مقاومت
مجاز خمشی نسبت به طراحی آنها اقدام نماید.
آرماتوربندی ( Reinforcement )
در سقف های مرکب عرشه فولادی دارای
تکیه گاه ساده تک دهانه، مش یا آرماتوربندی تنها
جهت جلوگیری از ایجاد ترک بوده و برای این منظور
حداقل مقدار آهن سقف 0/1 درصد از مساحت کل سقف میباشد.