کلید فولاد و معرفی فولادها و ویژگی ها و انواع فولاد و نام تجاری آنها
مقاله
در مورخ ۱۳۹۶/۰۵/۱۸
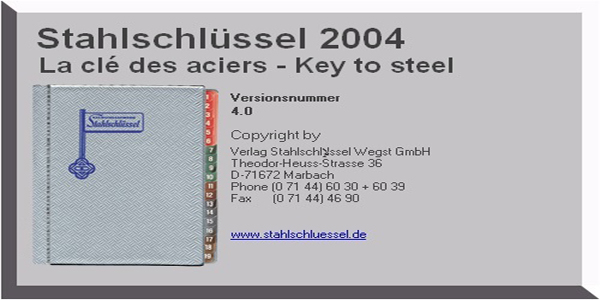
◄◄◄◄ مطلب شماره یک
در کلید فولاد، فولادها بر اساس خواص فیزیکی، شیمیایی، مکانیکی، نحوه تولید و یا کاربرد آن ها، در گروه های زیر دسته بندی شده اند:
1- گروه اول: فولادهای ساخت و ساز غیر آلیاژی (ساختمانی معمولی)، فولادهای سخت شونده سطحی یا سمانتاسیون، فولادهای نیتروره شونده و فولادهای خوش تراش یا اتومات
2- گروه دوم: فولادهای عملیات حرارتی پذیر، فولادهای بلبرینگ
3- گروه سوم: فولادهای فنر، فولادهای سخت شونده سطحی، فولادهای روزن کاری (اکستروژن) سرد
4- گروه چهارم: فولادهای چقرمه در دمای زیر صفر، فولادهای مخازن هیدروژن تحت فشار بالا، فولادهای مقاوم به حرارت برای ماشین سازی
5- گروه پنجم: فولادهای ریزدانه ساخت و ساز، فولادهای ساخت و ساز مقاوم در برابر هوا، فولادهای ریزدانه برای شکل دهی سرد
6- گروه هفتم: فولاد ابزار کربنی، فولادهای تندبر
7- گروه هشتم: فولادهای ابزار سرد کار
8- گروه نهم: فولادهای ابزار گرم کار
9- گروه یازدهم: فولادهای سوپاپ، فولادها و آلیاژهای مقاوم در دمای بالا
10- گروه دوازدهم: فولادهای غیر مغناطیسی، فولادهای نسوز، آلیاژهای رسانای حرارت
11- گروه سیزدهم: فولادهای زنگ نزن
12- گروه چهاردهم: فولادهای زنگ نزن ریختگی، فولادهای نسوز ریختگی
گروه اول:
1-1- فولادهای ساختمانی معمولی و غیر آلیاژی:
این فولادها در گروه فولادهای نرم (mild steel) با کربن کمتر از 25/0% (کم کربن) قرار می گیرند. در رده بندی استاندارد DIN EN 10027-2 جزء فولادهای پایه (Base steels) و رده تجاری با شماره مواد 1.00YY بوده و معمولاً بر اساس استحکام نهایی مشخص می شوند. فولادهای St 37، St 44، St 52 و St 60 از معروف ترین گریدهای این گروه از فولادها می باشد که در این نامگذاری طبق DIN 17006، عدد پس از St معرف استحکام کششی نهایی فولاد بر حسب Kg/mm2می باشد که با ضرب کردن آن در 81/9 مقدار استحکام نهایی بر حسب N/mm2 یا MPa به دست می آید. به عنوان مثال، استحکام کششی نهایی فولاد St 37 برابر Kg/mm2 37 یا حدود MPa 362 است. در این استاندارد، از اعداد 1 تا 3 برای رده بندی کیفیت فولاد پس از عدد مربوط به استحکام استفاده می شود، به عنوان مثال St 37-2، که عدد بزرگتر بیانگر شرایط بهینه فولادسازی و کاهش عناصر مضر است. در رده بندی کیفیت این فولادها، درجه 1 برای کارهای معمولی (معمولاً نوشته نمی شود)، درجه 2 برای کارهای مهم و درجه 3 برای فولادی که ریخته گری شده و دارای درجه خلوص بالا و خواص جوشکاری خوب است، استفاده می شود. در استاندارد DIN 17006 برخی پیشوندها و پسوندهایی جهت مشخص نمودن روش تولید یا بهینه سازی فولاد استفاده می شود، از جمله، پیشوندهای R و U (مثل USt 37 یا RSt 37) نماد فولاد کشته (اکسیژن زدایی شده) و کشته نشده (فولاد جوشان یا اکسیژن زدایی نشده) هستند.
با جایگزین شدن استاندارد DIN EN 10027-1 به جای استاندارد DIN 17006 و حذف این استاندارد، نامگذاری جدید این فولادها بدین صورت است که ابتدا حرف S و سپس استحکام تسلیم فولاد بر حسب MPa قید می شود و در ادامه در صورت نیاز، نمادهای عملیات حرارتی و یا نمادهای آزمون ضربه و سپس نمادهای اضافی جهت مشخص نمودن برخی شرایط ویژه ساخت، پوشش کاری و ... قید می شود. به عنوان مثال، S235JR معرف فولادی با تنش تسلیم MPa 235 است و نماد JR اشاره به این دارد که آزمون ضربه این فولاد در دمای C ْ 20 انجام گرفته و 27 ژول انرژی جذب شده است. نماد روتین ولی قدیم این فولاد St 37 می باشد. به عنوان مثالی دیگر، S355J2 معرف فولادی با تنش تسلیم MPa 355 است و نماد J2 اشاره به این دارد که آزمون ضربه این فولاد در دمای C ْ 20- انجام گرفته و 27 ژول انرژی جذب شده است. نماد روتین ولی قدیم این فولاد St 52 می باشد.
این دسته از فولادها، دارای خواص شکل پذیری سرد، جوشکاری و برشکاری عالی هستند و کاربرد اصلی آن ها با مقاطع مختلف ورق، میلگرد، تیرآهن، نبشی و انواع لوله، ساخت اسکلت های فلزی، انواع قطعات و ماشین آلات، اجزای ماشین و ... می باشد. به طور معمول، این فولادها به صورت محصول نهایی و تحت فرایندهای شکل دهی، برش و جوشکاری استفاده می شوند و عملیات حرارتی پذیر نیستند.
2-1-فولادهای سخت شونده سطحی یا سمانتاسیون
فولادهای این گروه معمولاً دارای کربن پایین بین 1/0 و 25/0 درصد هستند. اکثر فولادهای این دسته دارای عناصر آلیاژی منگنز، کروم، نیکل و مولیبدن و ... هستند. با افزودن کربن به سطح این فولادها به روش سمانتاسیون، آن ها قابلیت عملیات حرارتی کوئنچ و تمپر (چایش و بازگشت) و سخت کاری سطحی را پیدا می کنند. این فولادها به طور معمول در کاربردهایی استفاده می شوند که سطح نیاز به سختی بالا و مقاومت سایشی خوب و مغز نیاز به تحمل ضربه و چقرمگی خوب دارد، بنابراین در قطعات ساخت و ساز و اجزایی مثل قطعات پرسی و شکل پذیر، شغال دست، بوش، اتصالات، قطعات چرخ خیاطی و ماشین تحریر، چرخ دنده، پیستون، میل لنگ، محور و ... استفاده می شوند. نامگذاری این دسته از فولادها در استاندارد DIN بر حسب ترکیب شیمیایی آن ها انجام می گیرد. از جمله فولادهای مهم این گروه می توان به C10، C15، Ck10 و Ck15، 18CrNi8 (1.5920)، 16MnCr5 (1.7131) و ... اشاره کرد. در این نامگذاری ها C اشاره به عنصر کربن دارد و عدد پس از آن مقدار کربن فولاد است که در عدد صد ضرب شده است، یعنی C10 دارای 1/0% کربن است. حرف پس از C نیز بیانگر یک مشخصه خاص فولاد است. به طور مثال k، f، m و q به ترتیب بیانگر میزان فسفر و گوگرد پایین در ترکیب شیمیایی، مناسب برای سخت کاری شعله ای و القایی، میزان گوگرد 4/0-2/0% و مناسب برای فرم دهی سرد دارد. البته در استاندارد جایگزین شدهی DIN EN 10027-1 این نمادها تغییر یافته اند، به طور مثال در نامگذاری جدید به جای Ck10 از C10E استفاده می شود که E همان مفهوم میزان فسفر و گوگرد پایین در ترکیب شیمیایی فولاد را دارد. نامگذاری فولادهای کم آلیاژ سمانتاسیون نیز طبق استاندارد DIN EN 10027-1 بدین صورت است که ابتدا مقدار کربن با ضریب 10 نوشته می شود، سپس نماد عناصر عمده آلیاژی قید شده و مقدار آن ها با ضرایب مخصوص (مثلاً مقدار کروم، نیکل، سیلیسیم، منگنز، کبالت و تنگستن با ضریب 4، مقدار مولیبدن، مس، آلومینیوم، وانادیم و ... با ضریب 10، مقدار نیتروژن، گوگرد و فسفر با ضریب 100) نوشته می شود. به طور مثال 18CrNi8 به این مفهوم است که این فولاد میانگین 18/0% کربن، میانگین 2% (8 تقسیم بر 4) کروم و نیکل دارد. فولادهای سمانتاسیون در محصولات شرکت معتبر بوهلر (BOHLER) در گرید E طبقه بندی می شوند. به عنوان مثال E220 (نامگذاری قبلی بوهلر ECN 200 است) معادل 18CrNi8 (1.5920)، E410 (نامگذاری قبلی بوهلر EC80 است) معادل 16MnCr5 (1.7131) و E920 معادل Ck15 می باشد. معادل این فولادها در گریدبندی فولادهای پلدی (POLDI) به ترتیب CN18، CE2 و VARN است. در گریدبندی فولادهای زارشتال (ROSHLING) نیز معادل فولاد 1.5920 و 1.7131 به ترتیب فولادهای RECN و EC80 است.
3-1-فولادهای نیتروره شونده (Nitriding steels)
نیتروژن دهی عبارت از وارد کردن نیتروژن اتمی در لایه سطحی فولاد است. نیتروژن اتمی در سطح قطعه با برخی از عناصر آلیاژی ترکیب شده و تشکیل نیترید آلیاژی می دهد. در حقیقت سختی زیاد لایهی سطحی فولادهای نیتروژن داده شده ناشی از وجود همین ذرات بسیار ریز و پراکنده نیتریدهای آلیاژی است. در حالی که امکان نیتروژن دهی برای بسیاری از فولادها وجود دارد، تنها هنگامی می توان سختی زیاد در سطح به دست آورد که قطعه مورد نظر از جنس فولادهای آلیاژی شامل عناصر آلومینیوم، وانادیم، کروم و مولیبدن باشد. اگر فولادهای کربنی ساده نیتروژن دهی شوند، سختی سطح در حد متوسط (400 ویکرز) افزایش می یابد. دلیل این موضوع اینست که در دمای نیتروژن دهی، نیتروژن نسبتاً سریع به داخل فولاد نفوذ کرده و تشکیل Fe4N و گاهی Fe2N می دهد. از آنجایی که نیتریدهای یاد شده در عمق نسبتاً زیادی پراکنده می شوند، سختی سطح را نمی توانند در حد زیادی افزایش دهند. با حضور عناصر آلیاژی یاد شده، به دلیل میل ترکیب زیاد آن ها با نیتروژن، از نفوذ آن به داخل قطعه جلوگیری شده و روی قطعه یک لایهی نسبتاً نازک پایدار (تا حداکثر 1 میلی متر) و سخت نیتریدی تشکیل می شود. دو تفاوت اساسی روش نیتروره و کربوره اینست که اولاً کربن دهی باید در گستره دمایی آستنیت (875 تا 925 درجه سانتیگراد) انجام شود، در حالی که نیتروژن دهی را می توان در گستره دمایی فریت (550 تا 650 درجه سانتیگراد) انجام انجام داد. به علاوه پس از نیتروژن دهی نیازی به سریع سرد کردن قطعه نیست و معمولاً در هوا سرد می کنند. دمای پایین عملیات نیتروره، احتمال تاب برداشتن قطعات را کاهش می دهد، به همین علت برای قطعات پیچیده و حساس پیشنهاد می شود. ثانیاً عمق نفوذ نیتروژن در نیتروره کمتر از کربن در سمانتاسیون است. سختی سطحی فولادهای نیتروره معمولاً 800 تا 950 ویکرز می باشد. کاربرد این فولادها بیشتر در قطعات ماشین های صنعتی که تحت سایش قرار دارند، نظیر میله پیستون و قطعات در معرض بخار و اجزاء شیرها می باشد. این دسته از فولادها در رده بندی استاندارد DIN EN 10027-2 با شماره مواد 1.85YY مشخص می شوند. از جمله فولادهای این گروه می توان به فولادهای 31CrMoV9 (1.8519)، 34CrAlNi7-10 (1.8550) اشاره کرد. نحوه نامگذاری این فولادها طبق استاندارد DIN EN 10027-1 در بخش اول قسمت فولادهای سمانتاسیون شرح داده شد. فولادهای نیتروره در محصولات شرکت معتبر بوهلر (BOHLER) در گرید V طبقه بندی می شوند. به عنوان مثال فولاد V350 معادل 1.8519 و فولاد V820 معادل 1.8550 می باشد.
4-1-فولادهای خوش تراش یا اتومات (Free-cutting steels)
فولادهای خوش تراش یا اتومات فولادهای کم آلیاژی هستند که حضور عناصری چون فسفر، گوگرد و سرب به ترتیب با مقادیر کمتر از 1/0%، 4/0% و 35/0% سبب می شود که با رسوب این عناصر در مرزدانه ها، براده ها حین ماشینکاری خرد شده و با افزایش سرعت براده برداری، فولاد خوش تراش شده و پس از ماشینکاری کیفیت سطحی خوبی به دست آید. به دلیل حضور گوگرد و فسفر در ترکیب این فولادها، خواص مکانیکی ضعیفی دارند. برای بهبود خواص مکانیکی این فولادها، منگنز از مقدار 5/0 تا 7/1% در گریدهای مختلف آن حضور دارد. این فولادها به روش نورد گرم و یا کشش سرد تولید می شوند و آهنگری، شکل دهی سرد و جوشکاری نمی شوند. کاربرد این فولادها برای تراش اتوماتیک و سری تراشی جهت تولید انبوه قطعات اتومبیل و قطعات صنعتی است. این دسته از فولادها در رده بندی استاندارد DIN EN 10027-2 با شماره مواد 1.07YY مشخص می شوند. از جمله فولادهای این گروه می توان به فولادهای 9SMn28 (1.0715)، 9SMnPb28 (1.0718) و 45S20 (1.0727) اشاره کرد. معادل فولادهای خوش تراش 1.0715 و 1.0718 در گریدبندی محصولات شرکت بوهلر (BOHLER) عبارت از Z906 و Z950 است.
نویسنده: مهدی نقویان
◄◄◄◄ مطلب شماره دو
فولادهای ساختمانی معمولی : این فولادها جزء فولادهای غیرآلیاژی هستند و چون درانتخاب آن ها استحکام کششی نقشی تعیین کننده دارد ، آن ها را برحسب استحکام کششی شان طبقه بندی می کنند . استحکام کششی این فولادها متناسب با درصدکربن موجود در آنها افزایش می یابد و برعکس ، انبساط (کش آمدن ) آنها کاهش می یابد .، به عبارت دیگر، با افزایش کربن ، شکنندگی فولادبیشترمی شود . همچنین ازدیاد کربن قابلیت تغییر فرم درحالت یا گرم ، قابلیت جوشکاری ، و براده برداری فولاد را کاهش می دهد .
این فولادها از 0.12 تا 0.6 درصد کربن داشته وآنها رادرسه گروه با درجه مرغوبیت 1و 2 و 3 تولید و به بازار عرضه می کنند .
فولادهای دانه ریزمخصوص جوشکاری : این فولادها قابلیت جوشکاری خوبی دارند .
فولادهای سختکاری شونده (کربوریزه ) : ازاین فولادها برای ساختن قطعاتی استفاده میشود که بایستی دارای سطح خارجی سخت وقسمت داخلی (مغز ) نرم باشند. همچنین سطح آنها درمقابل سایش مقاوم بوده وقسمت داخلی آنها قابلیت تحمل خودرادرمقابل ضربه حفظ کند وشکننده نباشد . برای این منظور، ابتدا کربن سطح خارجی آن ها رابا روش های مختلف افزایش می دهند وسپس سختکاری می کنند . برای اینکه قسمت داخلی این فولادها پس ازسختکاری ، نرم باقی بماند ، باید مقداردرصد کربن آن ها از2.0 درصد کمترباشد
a = ماسوره ماشین بافندگی (C10) d = فنر کششی و پیچشی (C45)
b = میله و بوش(C15) e = فنر شمش (C45)
c = قطعه کلاچ پنجه ای (C35 ) f = میل لنگ (C60)
شکل 2 - نمونه هایی از موارد مصرف فولاد های سختکاری شونده سطحی
.
a = کولیس و سایر وسایل اندازه گیری (15Cr3) d = پروانه قایق (36Cr Ni Mo 4)
b = چرخ دنده ها(15Cr Ni6) e = پدال (40Mn 4)
c = درپوش منابع تحت فشاری (16Mn Cr5 ) f = دسته شاتون (30Cr Mo V9)
شکل 3 - نمونه هایی از موارد مصرف فولاد های سختکاری شونده سطحی آلیاژی
فولادهای بهسازی شونده : این فولادها جزء فولادهای ساختمانی هستند و2.0 تا 6.0 درصد کربن دارند . استحکام کششی ومقاومت این فولادها رامی توان به وسیله بهسازی ( سخت کردن وبرگشت دادن تا درجه حرارت 500 تا 700 سا نتیگراد ) افزایش داد فولادهای بهسازی شونده برای ساخت قطعاتی به کار می رود که درمعرض ضربه وبرخورد قراردارند .، مانند میل لنگ ها ، محورلنگ پرس های ضربه ای ومحور وسایل نقلیه .
فولادهای ازته شدنی (نیتروژه ) : این فولادها قابلیت جذب ازت را دارند وبه همین دلیل می توان سطح آ ن ها راپس از بهسازی به وسیله ی جذب سطحی ازت سخت کرد . این فولادها جزء فولادهای آلیاژی هستند وممکن است حاوی فلزاتی مانند کرم ، مولیبدن ، وانادیم ، نیکل وآلومینیوم باشند . وجود فلزاتی مانند کرم ، مولیبدن وآلومینیم قابلیت جذب ازت را درفولاد افزایش می دهند . ازاین فولادها درساخت قطعاتی استفاده می شود که نباید هنگام عملیات حرارتی پیچیدگی پیدا شود .
فولادها ی اتوما ت : این فولادها که به آ نها « فولادهای خوش تراش » نیز می گویند ، جزء فولادهای ساختمانی هستند . استحکام این فولادها برحسب درصد عناصر موجود در آن ها متفاوت است . در هنگام براده براری از این فولا دها ، براده های کوتاهی جدا می شوند وسطح خوبی را به دست می دهند . این ویژگی بیشتراز همه مرهون وجود گوگرد s) ) است که مقدار آن دراین گونه فولادها به 18.0 تا 0.4 درصد می رسد . وجود گوگرد باعث می شود که فولاد گرم شده ، شکننده شود هنگام براده برداری براده های کوتاهی به وجود آید . به همین دلیل درماشینهای اتومات که براد ه های بلند اختلا لات فراوانی ( مانند پیچیدن براده به دور ابزار وکار ، سا ییدگی وکم شدن دوام ابزار ) رابه وجود می آ ورند ، از فولادهای اتومات استفاده شود . شایان توجه است که وجود گوگرد زیاد دراین فولادها ، استحکام آ نها رادر مقابل ضربه کاهش می دهد . از دیگر معایب فولادهای اتومات عدم قابلیت جوشکاری وتغییر فرم سرد آ ن ها است . فولادهای اتوما ت ( بجزگوگرد ) دارای 07.0 تا 65.0 درصد ، 6.0 تا 5.1 درصد منگز 05.0 تا 40. درصد سیلیسیم هستند ودرصورتی که شکنندگی بیشتر براده وسطح مرغوبتر مورد نظر باشد ، 15.0 تا 3.0 درصد سرب نیز به آن می افزایند.
فولادهای فنر : فولادهای فنر علاوه بر استحکام کششی زیاد ، باید خاصیت الا ستیسیته خوبی داشته ودربرابر سایش وارتعاش نیز مقاوم باشند . وجود سیلیسیم درفولاد فنر خاصیت الا ستیسیته ووجود کرم استحکام ومقاومت درمقابل خوردگی را افزایش می دهد . این ویژگی ها تنها به درصد عناصر موجود در فولاد بستگی ندارد بلکه با وجود آن ها می توان به وسیله ی عملیات حرارتی وتغییر فرم درحالت سرد ، خواص آن را تغییر داده و ویژگی های مورد نظر را به دست آورد . فولادهای کربنی با 5.0 تا 1 درصد کربن ، 3.0 تا 4.0 درصد منگز و حداکثر 04.0 درصد گوگرد وفسفر درساخت فنرها کابرد زیادی دارند . برای سا خت فنرهای تخت یا مارپیچی که پس از سا خت تحت عملیات حرارتی قرار نمی گیرد ، فولادهای سخت کشیده یا نورد شده به کار می رود . از فولادهای کرم ووانادیم دار ، درساخت فنرهای بزرگ اتومبیل ولکوموتیو استفاده می شود . فولادهای سیسیلیم دار نیز در سا خت فنرهایی کاربرد دارند که استحکام ومقاومت ضربه ای زیاد از آن ها انتظار می رود . این فولادها به طور متوسط 4.0 درصد کربن ، 75.0 درصد سیسیایم ، 95.0 درصد منگنز با مس یا بدون مس دارند ولی مقدار سیسیلیم آن ها ممکن است تا 2 درصد نیز برسد . فولادهای منگنز دار مخصوص ساخت فنر خودروها محتوی 25.1 درصد منگنز ، 4.0 درصد کربن ، 2درصد منگنز ، و45.0 درصد کربن هستند . استحکام کششی این فولادها به شرط انجام عملیات حرارتی تا 1400 نیوتن برمیلیمتر مربع افزایش می یابد . فولادهای سیسیلیم منگنز دار دارای استحکام کششی زیاد تا حدود 1850 نیوتن بر میلیمتر مربع هستند . نوعی از این فولاد که 64.15 درصد کرم ، 38.4 درصد نیکل ، 68.2 درصد مولیبدن ، 1درصد منگنز ، 32.0 درصد سیسیلیم ، 12.0 درصد مس و14.0 درصد کربن دارد ، درساخت فنر موترهای جت وسایر مواردی که مقاومت در مقابل گرمای زیاد مورد نیاز است ، به کار می روند . نوع دیگری از فولاد فنر با 50 درصد کبالت ، 20 درصد کربن کرم ، 15 درصد ولفرام و10 درصد نیکل وحداکثر 15.0 درصد کربن ، ودر دمای 760 سانتیگراد ویژگی های خود را حفظ می کند .
فولادهای مخصوص : دامنه ی فولادهای مخصوص به قدری وسیع است که نمی توان درباره ی ویژگی های همه ی آن ها سخن گفت . این فولادها رابه سه گروه : فولادهای نسوز ، فولادهای ضد زنگ وفولادهای ضد مغناطیس ، تقسیم کرده ایم وهریک از آن ها را شرح می دهیم .
فولادهای نسوز ( مقوم درمقابل حرارت وگداختگی )
استحکام این فولادها تا دمای 600 درجه سانتیگراد تضمین شده است وتا دمای 800 درجه سانتیگراد نیز نمی سوزند. شایان توجه است که درمورد گداختگی وسوختن فولادها دو مطلب مهم مورد نظر است .
الف – مقاومت در مقابل تاثیر گاز هایی مانند اکسیژن و اکسیدهای کربن ، بخار آب وگازهای گوگرد دار دردماهای بالا .
ب – حفظ خواص مکانیکی در دماهای بالا ، این ویژگی ها بیشتر مرهون کرم موجود درآنها بوده و هر چه دمای کاری آن ها بیشتر باشد ، باید مقدار کرم بیشتری با آن ها آلیا ژ شود تا از سوختن (درشت دانه شدن ) فولاد جلوگیری کند . از این فولادها برای تهیه ورق ، لوله های تا سیسا ت دیگ های بخار ، پره های توربین های گازی و بخاری ، سوپاپ دود موتورهای احتراقی و ... استفاده می شود .
| ویژگی ها وکاربرد فولاد نسوز |
|
موارد استفاده | ویژگی ها | علامت اختصاری |
لوله داغ بخار آب | قابلیت جوشکاری خوب | 14 Cr Mo 4 |
سوپاپ های موتور های احتراقی | مقاوم در مقابل سایش و خورندگی | X 45 Cr Ni W 15 13 X 45 Cr Ni Si 19 10 |
قطعات کوره های صنعتی جعبه های بهسازی | مقاوم در برابر سوختن (تا 1200 درجه سانتیگراد) | X 15 Cr Ni Si 25 20
|
فولادهای ضد زنگ
در این فولادها کرم کرم نیکل نقشی تعیین کننده دارد ومقدارکرم موجود در آن ها نباید از 13 درصد کمتر باشد . این فولادها درمقابل خوردگی ، رطوبت هوا واغلب اسیدها وبازها مقاوم هستند وبرای تهیه ظروف ولوله های صنایع غذایی ، شیمیایی وشیرینی پزی مورد استفاده قرارمی گیرند . در فولادهای ضد زنگی که برای تهیه ظروف ولوله های حاوی موادغذایی از آن ها استفاده می شود ، به مقدار 2.0 تا 4.0 درصد مس نیز با آن آ لیاژ می کنند تا از تاثیر بوی بد فولاد روی مواد غذایی جلوگیری شود . این فولادها رامی توان از طریق براده برداری یا روش روش بدون براده برداری تغییر فرم داد و بخوبی جوشکاری کرد فولادهای ضد زنگ را می توان به وسیله پولیش دادن صیقل داد وکاملا پرداخت کرد .
فولادهای ضد مغناطیس
این فولادها دارای منگنز زیادی هستند (مانند فولاد X 50 Mn Cr 18 ) فولادهای ضد مغناطیس را می توان درحالت سرد بخوبی فرم داد وچنانچه تغییرفرم زیاد در آن ها مورد نیاز باشد ، باید عملات تابانیدن روی آن ها انجام گیرد . عمل تابانیدن این فولادها به این ترتیب است که ابتدا آن ها را تا 1000 درجه سانتیگراد گرم کرده وسپس در آب خنک سرد می کنند . این عمل باعث می شود که فولاد نرم و سمج شود . فولادهای ضد مغناطیس قابلیت براده برداری خوبی ندارد . ازاین گونه فولادها می توان X 8 Cr Ni 12 12 را نام برد که فولادی ضد زنگ ، ضد مغناطیس ، قابل کشش عمییق ( درقالب های کششی ) است وبخوبی صیقل می پذیرد . این فولادها برای تهیه قاب ساعت ، محفظه قطب نما کارد وچنگال وظروف تزیینی مورد استفاده قرارمی گیرند .
فولادهای ورق : فولادهای ورق رادر گروه های خیلی ظریف ، سفید وهمچنین ظریف ، متوسط ، خشن وورق دیگ سازی تولید می کنند . ورق های خیلی ظریف وسفید را از فولادهای غیر آ لیا ژی نرم با ضخامت های کمتر از 0.5 میلیمتر تولید می کنند . چربی سطح خارجی این فولادها را پس از تولید از بین می برند ،ۀ به همین دلیل می توان روی آن ها بخوبی رنگ کاری کرد وعملیات چاپ را انجام داد . ورق های سفیدی که درایران به حلبی معروفند ، قشر نازکی از قلع دارند .
ورق های ظریف برای کارهایی مانند کشش عمیق یا ایجاد نقش برجسته مناسب است وسطح خارجی آن رامی توان بخوبی گالوانیزه یا رنگ کرد . درجه خوبی این ورق ها رابرحسب اعدادی از 10 تا 14 نرم بندی کرده اند ، به عنوان مثال ، علامت St 10 برای ورق های با قابلیت کشش عمیق وSt 14 برای ورق هایی که قابلیت کشش خیلی خوبی دارند ، انتخاب کرده اند . برای نشان دادن عملیاتی که پس از نوردکاری روی ورق ها انجام می شود ،ازعددهای 01 ، 02،03،04،05 استفاده می شود . انواع ورق های ظریف ، درحالت های سرد وگرم شکننده نیستند ومقدار کربن آن ها از 1.0 تا 15.0 درصد است . این فولادها می توانند تغییر شکل دهند وقابلیت جوش ذوبی دارند . انواع 03،04،05 برای جوش نقطه ای ودرزی مناسب است ورق های متوسط وخشن را معمولا از فولادهای ساختمانی معمولی وهمچنین از فولادهای بهسازی شونده وسختکاری شونده سطحی تهیه می کنند . مخزن ها ولوله های تحت فشاری را که لازم است قابلیت جوش ذوبی داشته باشند ، ازفولادهای غیرآ لیاژِ می سازند . علائم مشخصه این فولادها HIV, HIII, HII, HI است . هرچه ععدهای به کاررفته درعلامت اختصاری بزرگتر باشد ، نشان دهنده ی افزایش درصد کربن و استحکام کششی آنها ست . این ورق ها به « ورق های دیگ سازی» معروف هستند .
فولادهای ابزارسازی
فولادهای ابزارسازی به فولادهایی می گویند که از آن ها درساختن ابزارهای براده برداری وبرش ( مانند چکش ، تیغه های دستگاه خم کن ، سنبه های خم وکشش ، قالب های کوره کاری ، قالب های ریخته گری ... ) استفاده می شود . درانتخاب فولادهای ابزار سازی استحکام کششی وانبساط چندان مورد توجه نیست بلکه قابلیت برش وسختی آنها بیشترمطرح است . این فولادها رابرحسب درصد عناصر موجود در آنها به فولادهای ابزارسازی غیر آ لیاژی ، کم آلیاژ وپر آ لیاژ تقسیم می کنند . فولادهای ابزارسازی راهمچنین برحسب مورداستفاده ( دمای کاری ) به فولادهای سردکاروگرمکار وبرحسب موادخنک کننده ای که درهنگام سختکاری آنها به کارمیرود به فولادهای آبی ،روغنی وهوایی تقسیم می کنند . فولادهای ابزارسازی غیرآ لیاژِ وکم آ لیاژدارای 5.0 تا 5.1 درصدکربن هستند . میزان کربن فولادهای ابزارسازی پرآلیا ژتا 2/2 درصد است . همه ی این فولادها (حتی آنها که غیر آلیاژی هستند ) جزء فولادها ی نجیب به حساب می آیند .، زیرا درجه خلوص بالایی دارند . فولادهای سردکارسماجت خوبی دارند ومقاومت آنها درمقابل ضربه ، فشاروسا ییدگی زیاد است . بااین فولادها میتوان مواد کاررابا یکی از روش های براده برداری یا بدون براده برداری تغییرفرم داد . فولادهای گرمکار دردماهای بالا دارای استحکام مکا نیکی ، ودوام برندگی زیادی هستند وبرای تهیه قا لب های کوره کاری ، ماتریس مخصوص تهیه نیمه ساخته ها و... به کارمیروند . بااین فولادها می توان قطعات فولادی ، فلزات سبک وسنگین رادرحالت گرم تغییرفرم داد.
فولاد ابزارسازی غیرآ لیاژِی : دراین فولادها مقدارکربن ( 5/0 تا 5/1 درصد ) نقش تعیین کننده د رمورد استفا ده آنها دارد وچرچه مقدارآنها بیشترباشد ، به همان نسبت سختی آنها افزایش می یابد . درجه حرارت سختکاری این فولادها از 760 تا 850 درجه سانتیگراد است . وپس از سردکردن درآ ب ، آنها رادردمای 200 تا 300 درجه سانتیگراد برگشت میدهند . دمای کاری این فولادها کمتراز 200 درجه سا نتیگراد است ودر200 درجه سا نتیگراد سختی خودرااز د ست میدهند به عنوان مثال فولادابزارسازی غیرآ لیاژی C150 W1 پس از سختکاری ، از فولادهای آ لیاژی نیز سخت ترمیشود ولی دردرجه حرارت حدود 200 درجه سانتیگراد سختی خودرااز دست می دهد فولاد ابزارسازی غیرآلیاژی رامیتوان دردمای 800 تا 1000 درجه سا نتیگراد کوره کاری کرد .
فولادابزارسازی کم آلیاژ : برای افزایش دوام برش واستحکام درحالت گرم ، فولادهای ابزارسازی رابا عناصری مانند کرم ، ولفرام ، نیکل ، منگنز ،مولیبدن ووانادیم آ لیاژ می کنند . مجموع درصد عناصر آ لیا ژی درفولادهای ابزارسازی کم آ لیاژ از 5 درصد کمتر است . براده برداری با این فولادها نسبت به فولادهای ابزار سازی غیرآ لیاژی با سرعت برشی بیشتری امکان پذیراست وسختی وقابلیت برش خودراتا 400 درجه سا نتیگراد حفظ میکنند . این فولادها رامی توان دردرجه حرارت های 900 تا 1100 درجه سا نتیگراد سختکاری کرد . درهر حال ، بایدتوجه داشت که شرایط سختکاری ، کوره کاری وعملیا ت دیگری که روی آنها انجام خواهد گرفت ، ازطرف کارخانه های تولیدکننده داده میشود ولازم است که شرایط مربوط بدقت رعایت شود .
فولادهای ابزارسازی پرآلیاژ : فولادهای ابزارسازی پرآ لیاژرامی توان به سه گروه : فولادهای سردکار، گرم کاروتندبرتقسیم کرد. این فولادها به دلیل داشتن عناصری مانند ولفرام ،مولیبدن ،وانادیم وکبا لت ، درمقابل سایش سختی ومقاومت خوبی دارند ومخصوصا وجود ولفرام باعث می شود که بتوانند سختی خودراتا دمای 550 درجه سا نتیگراد حفظ کند. این فولاها می توانند تا 2.2 درصد کربن داشته باشند. ومجموع سایرعنا صرآ لیاژی درآنها بایداز5 درصدبیشترباشد. به نوعی ازاین فولادها که برای ساختن ابزارهای براده برداری به کارمیروند ، « فولادتندبر » می گویند . بااین فولادها می توان باسرعت برشی بیشترازفولادهای ابزارسازی کم آ لیاژ براده برداری کرد . درجه حرارت سختکاری این فولادها رامی توان برحسب کاربرد و درصد عناصر موجود درآنها از 920 تا 1320 درجه سا نتیگراد انتخاب کرد وآنها را در روغن یا هوا سرد نمود ودر دمای 100 تا 670 درجه سانتیگراد برگشت داد. از آنجا که قیمت این فولادها گران است ، دربعضی موارد برای صرفه جویی ، آنها رابه صورت قطعاتی کوچک به بازارعرضه می کنند واز آنها تنها برای تامین لبه های برنده ابزاراستفاده می نمایند . برای این منظور، این قطعات راروی بدنه ای ازفولادساختمانی لحیم سخت کرده یا جوش می دهند.
نویسنده : م- مزارعی
◄◄◄◄ مطلب شماره سه
استاندارد ورق فولادهای سازه ای و عمومی
کاربرد این نوع ورق های فولادی در مصارف عمومی سازه ای و ساختمانی می باشد
استاندارد | گرید | مصرف |
ASTM A36 | A36 | ورق های فولادی ساختمانی |
ASTM A 568 ASTM A 635 ASTM A 830 | 1006, 1008, 1009, 1010, 1012, 1015, 1016, 1017, 1018, 1019, 1020, 1021, 1022, 1023, 1025, 1026, 1030, 1033, 1035, 1037, 1038, 1039, 1040, 1524 | ورق های فولادی کربنی و کم آلیاژ برای مصارف عمومی |
ASTM A 569 | Type A, B, C | ورق های فولادی کربنی، برای مصارف عمومی |
DIN 17100 | St33, St37, St44, St57 | ورق های فولادی ساختمانی و مصارف عمومی |
EN 10025 | S235, S275, S355 - R, JO, J2, K2 | ورق های فولادی ساختمانی و مصارف عمومی |
JIS G3132 | SPHT-1, SPHT-2, SPHT-3, SPHT-4 | ورق های فولادی برای تولید لوله و پروفیل |
JIS G3101 | SS300, SS400, SS490 | ورق های فولادی جهت مصارف عمومی |